Automotive Fasteners and Components: Meeting the Demands of the Modern Vehicle
- Brittany St. Clair
- Feb 12
- 8 min read
Disclaimer: The information provided in this blog is for general informational purposes only. Always consult a professional like Component Solutions Group for specific automotive fastening solutions tailored to your needs.
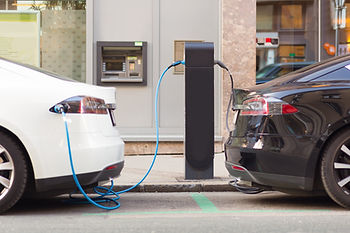
Recently, an automotive manufacturer approached us with a critical issue: their standard fasteners in an EV battery enclosure were corroding faster than expected, leading to safety concerns and potential sealing failures. The existing solution wasn’t holding up to the thermal cycling and moisture exposure in the vehicle’s undercarriage. By evaluating the materials and environmental stresses, we helped identify an alternative fastener with enhanced corrosion resistance and an optimized coating, extending the component’s longevity and ensuring a more secure battery housing.
This challenge highlights a growing reality in the automotive industry—fasteners are small but crucial components that must withstand extreme conditions while ensuring vehicle safety and performance. From preventing corrosion in harsh environments to maintaining integrity under constant vibration, fasteners play a vital role in modern vehicle design. As electric and autonomous vehicles push innovation forward, new demands for lightweight strength, electrical insulation, and enhanced durability continue to emerge.
As the industry evolves, manufacturers must rethink traditional fastener solutions to keep pace with advancements in electric vehicles (EVs), autonomous technology, and sustainability. The need for high-performance materials, vibration-resistant designs, and multi-functional fastening solutions has never been greater.
Let’s explore how the latest innovations in automotive fastening technology meet these new challenges.
Next-Gen Automotive Fasteners: Meeting New Challenges
The automotive sector is undergoing a seismic shift fueled by innovation in electric vehicles (EVs), autonomous technology, and a push for sustainability. Each advancement places unique demands on fasteners, prompting manufacturers to develop cutting-edge solutions.
Lightweighting and Material Advancements
Reducing vehicle weight is a priority for improving fuel efficiency and extending the range of EVs. This shift toward lightweight materials like aluminum, magnesium, and composites requires fasteners that can provide high strength without adding unnecessary bulk. Traditional steel fasteners may not always be compatible with these materials, risking galvanic corrosion or insufficient performance.
For instance, joining aluminum panels requires fasteners with enhanced corrosion resistance and durability. Manufacturers are increasingly turning to materials like titanium alloys and high-strength aluminum fasteners to meet these needs. The lightweight trend is underscored by industry growth; the global automotive lightweight materials market was valued at $100.8 billion in 2022 and is projected to grow at a CAGR of 11.2% through 2030, highlighting the increasing reliance on advanced fastener solutions.
Electric Vehicle Fasteners
Electric vehicles introduce new challenges for fastener technology. Unlike traditional internal combustion engine vehicles, EVs require fasteners that address unique factors like electrical conductivity, battery safety, and thermal management. For example, battery enclosures often need fasteners that provide secure sealing against moisture while withstanding the high thermal demands of lithium-ion cells.
Furthermore, fasteners in EVs must often incorporate features like electrical grounding or thermal insulation, making multifunctional designs a necessity. As the global EV market continues its meteoric rise, valued at $388.7 billion in 2022 and growing at a CAGR of 18.8%, the demand for innovative fastener solutions in this sector is at an all-time high.
Autonomous Driving and Sensor Integration
The advent of autonomous vehicles adds another layer of complexity to fastener design. These vehicles depend on an intricate web of sensors, cameras, and electronic components, all of which require secure and vibration-resistant fastening. Any failure in these systems could jeopardize the vehicle's ability to operate safely.
Fasteners for autonomous systems must ensure precise alignment, maintain reliability under constant vibrations, and sometimes even integrate with the sensor systems themselves. The autonomous vehicle market, projected to reach $1,802.8 billion by 2030 with a staggering CAGR of 32.4%, underscores the critical role of fasteners in supporting this growing technology.
By addressing these evolving demands with innovative materials and designs, fastener manufacturers such as Components Solutions Group are paving the way for the future of the automotive industry. From lightweight solutions to smart fasteners tailored for EVs and autonomous systems, the fastener industry remains at the forefront of automotive innovation.
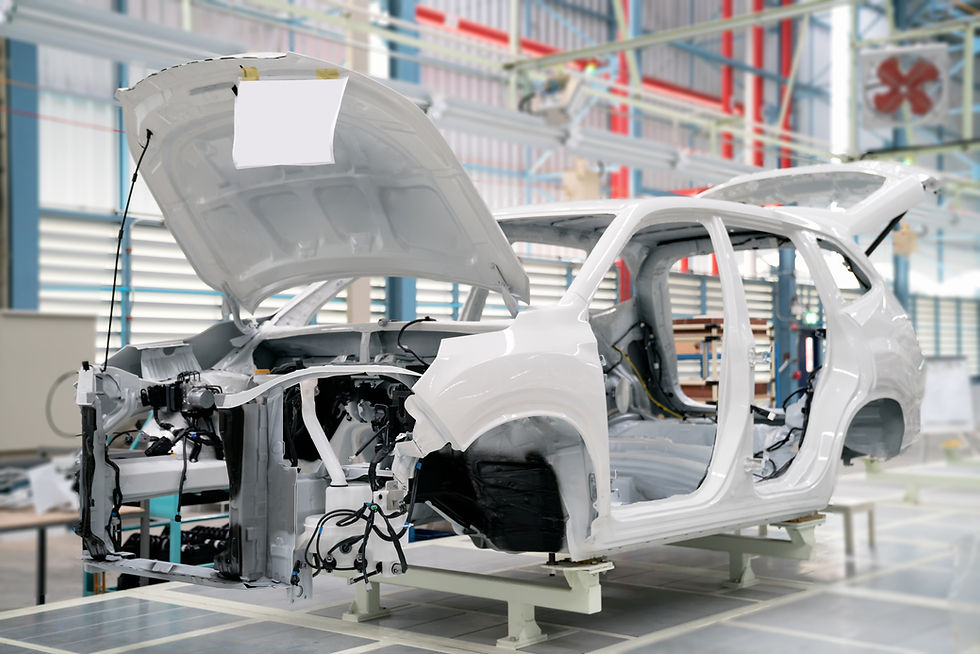
Addressing Key Challenges in Automotive Fastener Technology
As the automotive industry evolves, so do the challenges faced by engineers and manufacturers in designing and selecting fasteners. From resisting corrosion in harsh environments to maintaining integrity under constant vibration, each challenge demands tailored solutions to ensure safety, reliability, and efficiency.
Corrosion Resistance
Automotive fasteners are routinely exposed to environmental elements such as road salt, moisture, and chemicals, making corrosion resistance a top priority. Corrosion weakens fasteners, leading to potential failures in critical components like brake assemblies or suspension systems. Stainless steel fasteners and specialized coatings such as zinc-nickel plating or polymer coatings are commonly used to combat corrosion. Advanced solutions, like titanium fasteners or super duplex materials, offer even greater resistance for extreme conditions, such as in electric vehicle battery enclosures or off-road applications.
Vibration and Fatigue
Constant vibration and cyclic stress in vehicles can lead to fastener fatigue and eventual loosening, compromising the structural integrity of assemblies. This issue is especially critical in high-stress applications like engine mounts, wheel hubs, and drivetrain components. Engineers are increasingly utilizing fasteners with enhanced fatigue strength, such as those made from high-strength steel alloys, along with vibration-resistant locking mechanisms like serrated washers, lock nuts, or chemical thread-locking solutions.
Thermal Expansion
The diverse range of materials used in modern vehicles—aluminum, steel, and composites—creates a challenge when temperature fluctuations cause differing rates of thermal expansion. This can loosen fasteners or even cause them to fail under stress. High-temperature-resistant fasteners and designs that account for material compatibility and expansion rates are essential to address this issue. Advanced materials like Inconel or coated alloys are often used in applications such as exhaust systems or turbochargers where thermal expansion is pronounced.
Assembly Efficiency
Automotive manufacturers face increasing pressure to reduce production times and costs while maintaining precision. Efficient fastener solutions, such as automated installation systems or pre-assembled fastener kits, streamline assembly processes. Quick-release fasteners and self-clinching designs are also gaining popularity, particularly in applications requiring frequent maintenance or part replacement.
Quality Control and Traceability
Ensuring the reliability of automotive fasteners requires rigorous quality control measures. From raw material testing to precise dimensional tolerances, every step must adhere to industry standards such as ISO 9001 or IATF 16949. Additionally, manufacturers are adopting traceability systems with barcodes or RFID tags to monitor fasteners throughout their lifecycle, enabling quick identification and replacement in the event of a recall.
Cost Optimization
Balancing performance and cost remains a significant challenge. High-strength or corrosion-resistant fasteners often come with a premium price, making it necessary to evaluate their use in specific applications carefully. Bulk sourcing, partnering with trusted suppliers, and selecting cost-effective materials like coated carbon steel can help manufacturers optimize expenses without compromising safety or quality.
Environmental Impact
As sustainability becomes a focal point in the automotive industry, fastener manufacturers are exploring eco-friendly materials and processes. Recyclable fasteners, reduced waste during production, and coatings free of hazardous substances like cadmium are paving the way for a greener future. Manufacturers who embrace these practices not only reduce environmental impact but also align with global regulatory trends and consumer expectations.
The Impact of Regulatory Standards on Automotive Fasteners
Regulatory standards are the backbone of the automotive fastener industry, ensuring safety, reliability, and consistency across all applications. Standards like ISO 898 and SAE J429 define the mechanical properties that fasteners must meet to withstand stresses from vibration, thermal cycling, and extreme loads. These benchmarks reduce the risk of catastrophic failures, ensuring components like engine mounts, suspensions, and battery enclosures remain secure under demanding conditions. Additionally, global standards such as ISO 9001 and IATF 16949 promote compatibility and interchangeability, enabling manufacturers to source high-quality fasteners confidently from global suppliers. With the rise of electric and autonomous vehicles, emerging standards are addressing unique challenges, such as thermal management in EV battery enclosures and precise fastening for autonomous sensor systems.
Environmental regulations like RoHS and REACH are driving innovation in materials and coatings, encouraging the use of eco-friendly alternatives to traditional substances like cadmium. Moreover, regulatory requirements for traceability have led to the adoption of advanced tracking systems, ensuring that fasteners can be monitored throughout their lifecycle. These evolving standards not only enhance safety and reliability but also push manufacturers toward sustainable practices and innovative designs. For automotive OEMs and fastener suppliers alike, compliance with these benchmarks ensures access to global markets and maintains a competitive edge in a rapidly evolving industry.
Innovations in Automotive Fastener Design
The dynamic evolution of the automotive industry has sparked remarkable innovations in fastener technology. As vehicles become lighter, more efficient, and technologically advanced, fasteners must adapt to meet these new demands. From advanced materials to multifunctional designs, here’s how innovation is reshaping automotive fasteners.
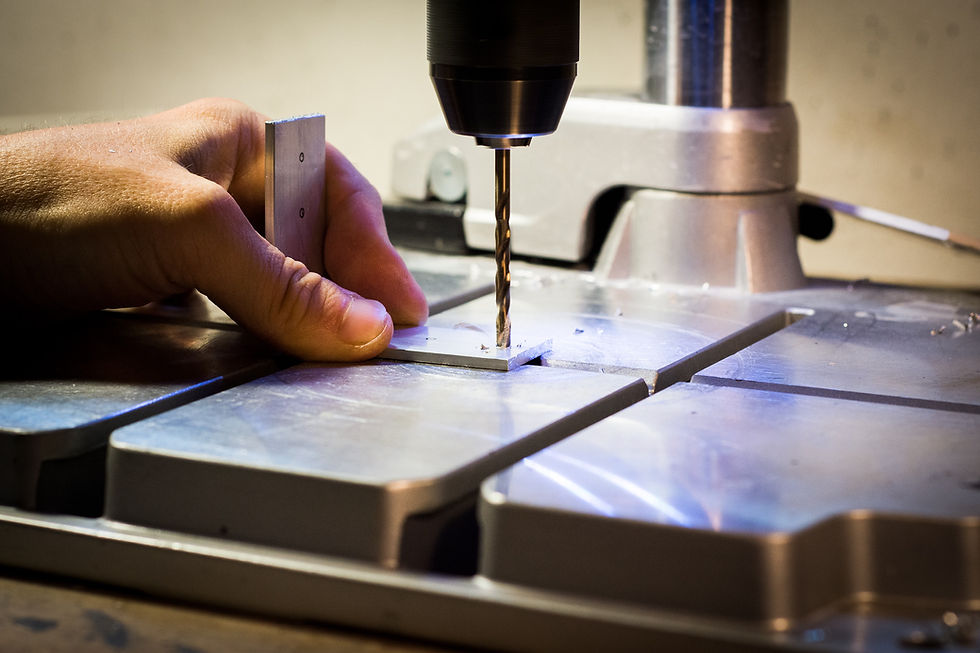
Advanced Materials
The shift toward lightweight vehicles requires fasteners that are not only strong but also compatible with advanced materials like aluminum, magnesium, and composites. High-strength steels and titanium fasteners are increasingly utilized for their superior tensile strength and weight-saving benefits. Composites, on the other hand, call for specially designed polymer fasteners or coated metals to ensure reliable connections without causing damage to the material. These materials also enhance performance in extreme conditions, such as high heat or corrosive environments.
Joining Technologies
Traditional methods of joining materials, such as welding or mechanical fastening, are now complemented by innovative techniques like adhesive bonding and clinching. These technologies provide stronger and more seamless assemblies, particularly in areas where traditional fasteners may be impractical. For instance:
Laser Welding: Ideal for high-precision assemblies in electric vehicle battery packs.
Structural Adhesive Bonding: Used to join dissimilar materials like aluminum and composites, ensuring durability without adding weight.
Clinching: A mechanical joining technique that eliminates the need for pre-drilled holes, speeding up assembly and reducing material waste.
Smart Fasteners
The rise of autonomous and connected vehicles has spurred the development of smart fasteners equipped with sensors. These fasteners monitor critical parameters like stress, temperature, and vibration, providing real-time data to ensure safety and performance. Applications include:
Stress monitoring in structural components.
Temperature tracking in high-heat areas like engines and exhaust systems.
Vibration detection in suspension assemblies to prevent loosening or failure.
Multifunctional Fasteners
Efficiency is key in modern automotive design, and multifunctional fasteners are at the forefront of this trend. By combining multiple functions, these fasteners reduce the need for additional components, streamlining assembly and cutting costs. Examples include:
Grounding and Sealing Fasteners: Provide both electrical grounding and water-tight sealing in EV battery enclosures.
Integrated Cable Management Fasteners: Secure wiring harnesses while maintaining structural integrity in tight spaces.
The Bottom Line: Driving Innovation with Automotive Fasteners
As the automotive industry evolves, fasteners continue to play a pivotal role in meeting the demands of modern vehicles. From lightweight materials and electric vehicles to autonomous driving systems, the right fasteners ensure safety, efficiency, and durability in every application. Manufacturers can stay ahead in this rapidly transforming landscape by embracing cutting-edge materials, smart technologies, and sustainable practices.
At Component Solutions Group (CSG), we are proud to be a leading provider of high-quality fasteners, offering precision-engineered solutions to meet the unique challenges of the automotive industry. Trust CSG to deliver innovative fastening systems that drive reliability and performance.
Contact us today to discuss how we can support your goals and overcome component challenges.
Frequently Asked Questions (FAQs)
What are the most common types of automotive fasteners?
In the automotive world, fasteners like bolts, screws, rivets, and clips are essential. Each type serves a unique purpose, from securing engine components to assembling interiors, ensuring every part stays in place under various conditions.
What are the risks of using the wrong fasteners in automotive applications?
Using the wrong fasteners can lead to serious issues like component failure, safety hazards, or expensive repairs. Incorrect materials or sizes may compromise structural integrity, especially in high-stress or corrosive environments.
How do I choose the right automotive fastener for my application?
Selecting the right fastener depends on factors like material compatibility, load requirements, and environmental conditions. Consulting a fastener selection guide or an expert ensures you get the perfect match for your project.
What are the challenges of using fasteners in electric vehicles?
Electric vehicles require fasteners that address unique needs like electrical conductivity, thermal management, and lightweight designs. Fasteners must also secure battery enclosures while maintaining safety and efficiency.
How are automotive fasteners evolving with autonomous driving?
With autonomous driving, fasteners must securely integrate sensors, cameras, and other advanced systems. They’re designed for precision and reliability to handle vibrations, environmental exposure, and consistent performance.
What are the latest advancements in automotive fastener coatings?
Fastener coatings now offer enhanced corrosion resistance, anti-vibration properties, and reduced friction. Innovations like ceramic and zinc-aluminum coatings help extend lifespan and improve performance in harsh conditions.
How can I ensure the quality and reliability of automotive fasteners?
Ensuring fastener quality involves adhering to strict standards, performing rigorous testing, and selecting reliable suppliers. Quality control measures, like torque testing and material certifications, guarantee safety and reliability in every application.