Winning the War on Corrosion: The Power of Corrosion Resistant Fasteners
- Brittany St. Clair
- Mar 7
- 5 min read
Updated: Mar 11
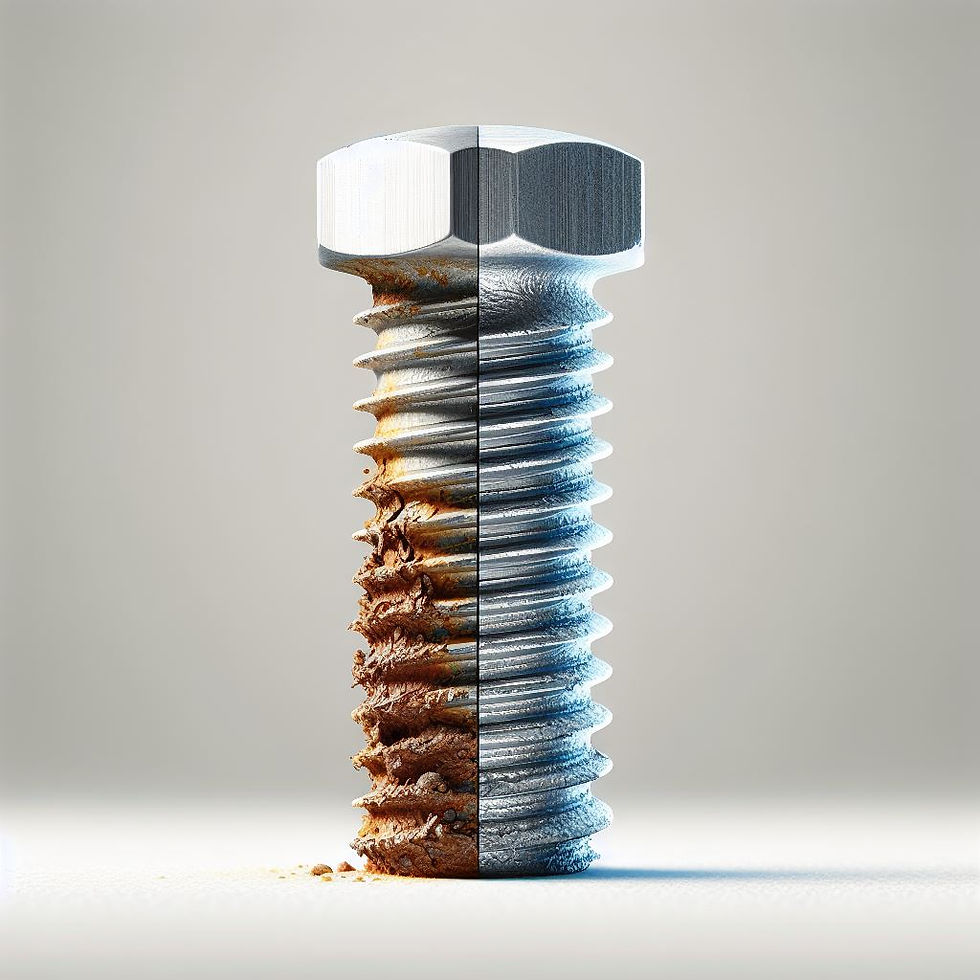
Corrosion is one of the most persistent and costly challenges industries face today. From offshore wind energy and aerospace to automotive and heavy machinery, the degradation of metal components leads to equipment failure, increased maintenance costs, and serious safety risks. Fasteners are among the most vulnerable elements, and they play a critical role in structural integrity and operational safety.
At Component Solutions Group (CSG), we specialize in high-performance, corrosion resistant fasteners engineered for extreme environments. Our goal is to help businesses mitigate corrosion risks, extend the lifespan of critical components, and ultimately reduce long-term operational costs.
A prime example is our work with Bladt Industries, a global leader in offshore wind turbine foundations. Facing severe corrosion challenges, they turned to CSG for a long-term solution—an in-depth analysis follows later in this article.
Understanding Corrosion
What is Corrosion?
Corrosion is the gradual deterioration of metal caused by chemical reactions with
environmental elements such as oxygen, moisture, salt, and industrial pollutants. Over time, these reactions weaken metal components, causing surface degradation and structural failure.
Why Corrosion is a Global Concern
The impact of corrosion is staggering, with the global cost exceeding $2.5 trillion annually, according to studies by NACE International. Key consequences include:
Increased Maintenance Costs: Frequent repairs and premature part replacements.
Unexpected Equipment Failures: Resulting in unplanned downtime and lost productivity.
Shortened Component Lifespan: Leading to increased material and labor costs.
Safety Hazards: Corrosion-induced failures can cause catastrophic accidents, especially in high-risk industries such as aerospace, oil & gas, and marine.
Unplanned Downtime & Production Loss: Downtime can cost $10,000–$50,000 per hour, while failure incidents can lead to $600,000+ in production losses.
Frequent Corrosion & Replacement Costs: Standard fasteners corrode quickly in harsh environments, leading to replacement costs that can exceed 3x the initial cost.
Increased Safety & Compliance Risks: Corrosion-related failures increase injury risks, liability claims, and regulatory violations, with legal fines exceeding $75,000+ per incident.
Environmental & Sustainability Issues: Corroding fasteners contribute to C-part sustainability issues, such as metal waste, structural contamination, and increased carbon footprints. Regulatory restrictions may limit material use in the future, increasing compliance costs.

Types of Corrosion in Fasteners
Different types of corrosion impact fasteners in various ways:
Uniform Corrosion: Gradual deterioration affecting the entire surface.
Pitting Corrosion: Small, deep holes that compromise integrity.
Crevice Corrosion: Forms in tight spaces where moisture accumulates.
Galvanic Corrosion: Occurs when two dissimilar metals interact in a corrosive environment.
Intergranular Corrosion: Weakens metal along grain boundaries.
Stress Corrosion Cracking (SCC): A combination of stress and corrosive exposure leading to sudden failures.
The Science of Corrosion Resistance
What is Corrosion Resistance?
Corrosion resistance refers to a material’s ability to withstand exposure to chemical and environmental elements without significant deterioration. Industries rely on corrosion resistant solutions to maintain operational efficiency and safety.
Factors That Influence Corrosion Resistance
Material Composition: Stainless steel, titanium, and aluminum alloys naturally resist corrosion.
Environmental Conditions: Factors such as humidity, temperature, and chemical exposure accelerate corrosion.
Coatings and Treatments: Protective layers like galvanization, powder coatings, and anodization enhance durability.
Ways to Prevent Corrosion in Fasteners
Evaluate the Environment: Assess the likelihood of accumulated deposits that may lead to corrosion.
Optimize Design: Optimize designs leveraging DFM practices to minimize crevice formation and moisture retention.
Material Selection: Opt for corrosion resistant alloys such as super duplex stainless steel.
Protective Coatings: Apply zinc (galvanization), epoxy, or powder coatings to create a barrier.
Avoid Mixed Materials: Prevent galvanic corrosion by avoiding materials with a large difference in electrode potential.
Industries Most Affected by Corrosion
1. Offshore Wind Energy & Marine Industries
Saltwater exposure accelerates corrosion, leading to frequent failures in fasteners used in offshore wind turbines and marine applications.
2. Aerospace & Aviation
High-altitude moisture and temperature fluctuations cause metal degradation, making corrosion resistant fasteners essential for aircraft safety.
3. Automotive & Heavy Machinery
Road salt, humidity, and industrial chemicals increase corrosion risks in vehicle and construction fasteners.
4. Oil & Gas Industry
Pipelines and rigs face extreme conditions that demand high-performance, corrosion resistant fasteners to prevent leaks and structural damage.
Choosing the Right Corrosion Resistant Fasteners
BUMAX – The World’s Strongest Stainless Steel Fastener
BUMAX fasteners are recognized as the world’s strongest stainless steel fasteners, offering exceptional corrosion resistance and mechanical strength in aggressive environments.
Case Study: Bladt Industries & the Cost Savings of BUMAX SDX 109
Bladt Industries is a global leader in offshore wind turbine foundations, facing severe corrosion challenges in their marine environments.
Challenge: Frequent fastener failure due to severe marine corrosion.
Solution: Implementation of BUMAX SDX 109 corrosion resistant fasteners.
Results:
Significant Maintenance Cost Reduction: Lower routine inspections and replacements.
Extended Turbine Lifespan: 27+ years of structural integrity.
Enhanced Reliability: Higher tensile strength, minimizing downtime.
Sustainability Benefits: Reduced replacements lower material waste and carbon emissions.
Implementing BUMAX SDX 109 corrosion resistant fasteners significantly improved structural durability and reduced maintenance costs. View the full case study here.

Types of BUMAX Fasteners and Their Applications
BUMAX® 88 – Superior corrosion resistance for marine applications.
BUMAX® 109 – Strongest A4 stainless steel fastener.
BUMAX® DX 129 – High-strength duplex stainless steel.
BUMAX® SDX 109 – Super duplex grade for extreme corrosion resistance.
BUMAX® ULTRA – Precipitation-hardenable stainless steel for ultra-high strength.
BUMAX Fastener Products
Hexagon Head Bolt & Screw – High-strength applications.
Stud & Stud Bolt – Custom-made for demanding conditions.
Hexagon Nut – Durable and corrosion resistant.
Thread Forming Screw – Self-tapping in stainless steel sheets.
Lock Nuts & Washers – Improved load distribution and secure fastening.
Other High-Performance Fastener Options
Super Duplex Stainless Steel: Superior strength and corrosion resistance.
Titanium Fasteners: Lightweight and exceptionally resistant to seawater corrosion.
Best Practices for Fastener Selection
Consider the operating environment (humidity, chemicals, temperature).
Assess the mechanical stress and required load-bearing capacity.
Choose coatings and treatments based on exposure risks.
The Cost of Corrosion & Long-Term Savings
The Hidden Costs of Corrosion
Corrosion results in both direct costs (repairs, replacements) and indirect costs (downtime, safety liabilities). Unchecked corrosion increases liability risks, regulatory fines, and unexpected maintenance expenditures.
How Corrosion Resistant Fasteners Save Money
Reduced Maintenance Cycles – Lower labor and material costs.
Extended Equipment Lifespan – Maximizing return on investment.
Fewer Failures = Higher Operational Efficiency – Minimizing unplanned downtime.
Future of Corrosion Resistance & How CSG Can Help
Corrosion remains a significant industrial challenge, but the right strategies and materials can dramatically reduce its impact. Investing in corrosion resistant fasteners enhances safety, reliability, and long-term cost savings.
At Component Solutions Group, we provide high-performance fasteners, including BUMAX, that withstand the most demanding environments.
📩 Contact us today for expert guidance on corrosion resistant solutions tailored to your industry needs!
#Corrosion #CorrosionResistance #Fasteners #BUMAX #BUMAXFasteners #CorrosionSolutions #HighPerformanceFasteners #IndustrialFasteners #OffshoreFasteners #StainlessSteel #StainlessSteelBolts