Flange Bolts: Challenges, Sizing, Torque Specs (ASME B16.5), and Applications
- Brittany St. Clair
- Dec 3, 2024
- 11 min read
Updated: Jan 2
Disclaimer: The information provided in this blog serves as a general guide for flange bolt selection, sizing, and installation. While every effort has been made to ensure accuracy, the specific requirements of your application may vary based on variables such as material properties, operating conditions, and environmental factors. Users are responsible for verifying the suitability of flange bolts for their specific needs and must refer to ASME B16.5 standards or consult with professionals for precise calculations and applications.
Flange bolts are indispensable in industrial systems, providing the critical clamping force needed to secure flanges and create leak-proof connections. These fasteners play a pivotal role in maintaining system integrity, especially in high-pressure and high-temperature environments where even minor failures can have significant consequences. By forming the backbone of structural and fluid systems, flange bolts ensure the safe and efficient operation of pipelines, pressure vessels, and other essential components.
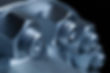
However, improper selection or installation of flange bolts can result in severe issues, including leaks, compromised system integrity, and costly downtime. Challenges such as selecting the correct size, adhering to torque specifications outlined in ASME B16.5, and ensuring material compatibility must be addressed to prevent failures and maintain performance. A thorough understanding of these factors is key to achieving long-lasting, reliable bolted connections that meet the demands of industrial operations.
What are Flange Bolts?
Flange bolts are specialized fasteners designed to connect two flanges—flat, disc-like components with evenly spaced pre-drilled holes. Tightening flange bolts creates a compressive force that secures the flanges together, with a gasket often placed in between to create a leak-proof seal. This design ensures the safe containment of gases, liquids, or other substances under varying pressures and temperatures.
Key Features of Flange Bolts
High Strength: Flange bolts are manufactured using robust materials like stainless steel, alloy steel, or other corrosion-resistant alloys to handle significant mechanical loads, extreme temperatures, and aggressive environments.
Stud Bolts: Often used in flange applications, stud bolts are threaded rods paired with nuts at both ends, providing secure and evenly distributed clamping force across the flange face.
Gaskets: The incorporation of gaskets—compressible materials like PTFE, graphite, or rubber—is critical in ensuring a leak-proof seal between the flanges.
These features enable flange bolts to maintain mechanical stability, even in the most demanding industrial settings.
Importance of Flange Bolts
Flange bolts are indispensable in industries that require secure, high-performance connections to prevent leaks and ensure operational safety:
Oil and Gas Industry: Flange bolts are integral in pipelines, refineries, and offshore platforms, where high pressures and temperatures are common. Failure to use the right flange bolts can lead to catastrophic leaks and safety hazards.
Chemical Processing: In chemical plants, flange bolts hold together tanks, reactors, and piping systems, ensuring they withstand corrosive substances and prevent hazardous leaks.
Power Generation: Boilers, turbines, and other power plant equipment rely on flange bolts for secure assembly and efficient operation under extreme thermal conditions.
Water Treatment: Flange bolts in pipelines and valves play a critical role in distributing water safely and efficiently, while preventing system failures in treatment facilities.
Challenges in Flange Bolt Selection and Installation
Flange bolts are the backbone of many industrial systems, ensuring secure, leak-proof connections in piping, machinery, and other critical applications. However, improper selection or installation can lead to costly failures, jeopardizing safety and operational efficiency. Key challenges include sizing, torque application, material compatibility, and environmental considerations. Addressing these factors is essential to maintain system integrity and prevent leaks or damage.
Sizing
Selecting the correct size for flange bolts is fundamental to achieving a secure seal. Bolts that are too short may not provide adequate clamping force, while bolts that are too long can damage the flanges or interfere with other components. Proper sizing ensures even distribution of pressure across the flange and gasket, minimizing the risk of leaks. Referencing standards such as ASME B16.5 is crucial to identifying the appropriate bolt size based on the flange class, pressure rating, and material used.
Read also: How to Measure Bolt Size Accurately
Torque Specifications
Applying the correct torque is critical to ensuring that flange bolts provide the necessary clamping force without over-tightening or under-tightening. Over-tightened bolts can deform the flange, damage the gasket, or compromise the bolt's integrity, while under-tightened bolts may lead to leaks and system instability. Adhering to the torque specifications provided in ASME B16.5 ensures precise force application. Using a calibrated torque wrench and tightening incrementally in a cross-pattern sequence further helps achieve uniform pressure on the gasket.
Gasket Selection
The gasket is a key component in creating a leak-proof seal between flanges, but its performance heavily depends on proper material selection and installation. Gaskets that are incompatible with the operating environment can fail under high pressure, extreme temperatures, or exposure to corrosive substances. Proper alignment and compression during installation are also critical to ensuring a uniform seal. Selecting gaskets made of materials like PTFE, graphite, or elastomers based on the specific application minimizes the likelihood of failure.
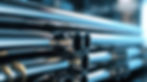
Bolt Material
Flange bolts must be made from materials that can withstand the environmental and operational stresses of the system. Incompatible bolt materials may corrode, gall, or crack under high loads or extreme conditions, compromising the joint's integrity. Stainless steel and alloy steel are common choices for their strength and corrosion resistance. It’s vital to match the bolt material with the flange and gasket materials to ensure compatibility, especially in systems exposed to aggressive chemicals or
temperature fluctuations.
Thermal Expansion
Temperature changes in industrial systems can cause thermal expansion or contraction of the flanges, bolts, and gaskets. These variations can alter the clamping force, leading to leaks or joint instability. Systems operating under extreme thermal conditions require materials that can accommodate these expansions and maintain consistent performance. Flexible gaskets and techniques like using spring washers can help mitigate these effects.
Lubrication
Neglecting proper lubrication of flange bolts during installation can result in excessive friction, leading to inaccurate torque readings and potential damage. Lubrication reduces thread friction, ensures smoother tightening, and prevents galling, especially in stainless steel bolts. Applying a suitable thread lubricant not only improves torque accuracy but also enhances the longevity of the bolts and flanges.
Vibration
Industrial environments often expose flange connections to high levels of vibration, which can cause bolts to loosen over time. This loosening compromises the seal, leading to leaks and potential system failures. To address this, locking mechanisms such as lock washers or prevailing torque nuts are used to secure the bolts. Additionally, implementing vibration-dampening measures reduces the risk of joint loosening.
By understanding and addressing these challenges, you can ensure the successful selection and installation of flange bolts, safeguarding the performance and reliability of your systems. Proper sizing, torque application, material compatibility, and attention to environmental factors are key to achieving leak-proof and durable connections.
Flange Bolt Size Charts (ASME B16.5)
Understanding ASME B16.5
ASME B16.5 is a globally recognized standard that provides comprehensive guidelines for the design, dimensions, and pressure ratings of pipe flanges and flanged fittings. One of its key aspects is detailing bolt sizes, materials, and configurations for various flange classes. By adhering to ASME B16.5, industries ensure that flange connections are safe, compatible, and properly sealed under pressure. This standard eliminates guesswork, ensuring that all components—flanges, bolts, and gaskets—work together seamlessly.
Compliance with ASME B16.5 is not just a technical requirement but a crucial safety measure. Missteps in bolt selection or flange compatibility can lead to catastrophic failures, leaks, or even environmental hazards, particularly in high-stakes industries like oil and gas, chemical processing, and power generation.
Key Parameters in Size Charts
Flange bolt size charts provide essential information to help engineers and technicians select the correct bolts for specific applications. Some of the primary parameters included in these charts are:
Nominal Pipe Size (NPS): The standard dimension that identifies the pipe’s diameter.
Flange Class: Pressure ratings (e.g., Class 150, 300, 600) that dictate the strength of the flange.
Bolt Diameter: The diameter of the bolts required to secure the flange.
Number of Bolts: The total number of bolts necessary to complete the connection.
Bolt Circle Diameter: The distance between the centers of bolt holes in the flange.
Bolt Length: For stud bolts, this includes the thread length and any protrusion required for nuts.
Understanding these parameters ensures accurate bolt selection and compatibility with flanges, gaskets, and nuts.
Interpreting Size Charts
Reading flange bolt size charts can seem complex at first, but a clear process simplifies it:
Identify the Nominal Pipe Size (NPS) for your application.
Determine the Flange Class based on the pressure and temperature requirements.
Cross-reference these values in the chart to find the appropriate bolt diameter, number, and length.
For example, if you are working with a Class 300 flange for a 6-inch NPS, the chart might specify 8 bolts with a diameter of 3/4 inches and a bolt circle diameter of 9.5 inches. Accurate interpretation ensures a proper fit and reliable performance.
Accessing ASME B16.5 Size Charts
For complete and official size charts, refer to the ASME B16.5 documentation, which is available for purchase through ASME or licensed distributors. Many manufacturers and suppliers also provide simplified versions of these charts for quick reference, tailored to their product offerings.
Flange Bolt Specs (ASME B16.5)
Bolt Material Specifications
ASME B16.5 specifies approved materials for flange bolts to ensure they can withstand demanding industrial conditions. Common materials include:
Alloy Steel: Known for its high strength and ability to endure elevated pressures.
Stainless Steel: Offers excellent corrosion resistance, making it ideal for chemical and marine applications.
High-Strength Alloys: Materials like ASTM A193 Grade B7 or A320 Grade L7 are engineered for extreme temperatures and pressures.
Selecting the right material depends on the operating environment. For instance, applications in chemical plants require corrosion-resistant bolts, while those in high-temperature systems need heat-resistant materials.
Thread Specifications
Thread type and pitch are critical for flange bolt performance, ensuring secure and compatible connections between bolts and nuts. ASME B16.5 typically specifies threads as Unified National Coarse (UNC) or Unified National Fine (UNF), depending on the application. Coarse threads are common for general use, while fine threads offer enhanced strength and are preferred in high-stress environments.
Mechanical Property Specifications
To maintain the integrity of flange connections, ASME B16.5 outlines minimum mechanical properties for flange bolts:
Tensile Strength: The maximum stress a bolt can endure before breaking.
Yield Strength: The stress level at which a bolt begins to deform permanently.
Hardness: Resistance to deformation and wear, ensuring bolts can handle long-term use under pressure.
These mechanical properties are vital for ensuring bolts can handle operational loads without failing.
Other Specifications
ASME B16.5 also addresses other important aspects, such as:
Bolt Head Dimensions and Markings: Ensures bolts meet dimensional standards and include grade markings for easy identification.
Nut Dimensions and Markings: Specifies the size and threading requirements for compatible nuts.
Washer Dimensions and Materials: Details the appropriate washer sizes and materials to distribute load effectively.
Adherence to these specifications minimizes the risk of mismatched components and ensures a secure assembly.
Importance of Compliance
Compliance with ASME B16.5 is non-negotiable in safety-critical applications. By using flange bolts that meet these stringent standards, you reduce the risk of leaks, joint failures, and costly downtime. Properly specified and installed flange bolts provide the reliability and peace of mind required in high-pressure environments, from pipelines to power plants.
Applications of Flange Bolts
Flange bolts are critical components across a broad spectrum of industrial applications, ensuring secure, leak-proof connections in high-pressure and high-stress environments. Their strength, durability, and reliability make them indispensable in maintaining operational efficiency and safety.
Piping Systems
Flange bolts connect pipes, valves, and pumps in industrial piping systems, ensuring leak-proof seals under high-pressure and high-temperature conditions. They are essential for transporting water, oil, gas, or chemicals while
enabling easy maintenance by allowing disassembly and reassembly without damage.

Pressure Vessels
Used in reactors, storage tanks, and boilers, flange bolts secure components and contain fluids or gases under extreme pressures and temperatures. Proper material and torque specifications ensure a durable seal, minimizing the risk of failure.
Heat Exchangers
Flange bolts maintain tight seals between heat exchanger sections, preventing leaks and cross-contamination while ensuring energy efficiency. Their role is crucial in power generation, chemical processing, and HVAC systems.
Oil and Gas Industry
Designed for harsh conditions, flange bolts secure pipelines, refineries, and offshore platforms. They withstand corrosive substances, extreme temperatures, and subsea challenges, ensuring system integrity in demanding environments.
Chemical Processing
Flange bolts in chemical plants secure tanks and pipelines, containing toxic or corrosive substances. Their resistance to chemicals, temperature fluctuations, and pressure ensures system integrity and safety for personnel and the environment.
Water Treatment Facilities
In water treatment plants, flange bolts connect pipelines, valves, and pumps, ensuring leak-proof joints capable of withstanding mechanical stresses and high flow rates. Corrosion-resistant bolts are critical for long-term reliability.
Industrial Machinery
Flange bolts provide structural integrity to heavy machinery such as turbines and compressors, maintaining secure connections under heavy loads and dynamic conditions. Their reliability reduces downtime and prevents failures.
By tailoring flange bolt selection to specific application needs, industries can ensure long-lasting performance, safety, and operational efficiency across diverse systems and equipment.
Choosing the Right Flange Bolt: A Recap
Selecting the correct flange bolt is a critical step in ensuring the integrity and safety of industrial systems. By understanding the challenges and considering factors like sizing, torque specifications (ASME B16.5), material compatibility, and environmental conditions, you can make informed decisions that lead to reliable and leak-proof connections. Remember to refer to ASME B16.5 for detailed guidance on flange bolt dimensions, materials, and installation procedures.
The Bottom Line:
Flange bolts are indispensable in a wide range of applications, from piping systems and pressure vessels to heat exchangers and industrial machinery. Their ability to withstand high pressures, temperatures, and corrosive environments makes them essential for maintaining operational efficiency and preventing costly failures. By prioritizing proper selection, installation, and maintenance practices, you can ensure the long-term performance and safety of your flange connections.
Frequently Asked Questions (FAQs)
What are flange bolts?
Flange bolts are high-strength fasteners specifically designed to connect flanges, creating a sealed joint in industrial piping and mechanical systems. They work in tandem with gaskets to prevent leaks and maintain structural integrity under high pressure and temperature conditions. Their strength and durability make them essential in applications like oil and gas, chemical processing, and water treatment facilities.
What is ASME B16.5?
ASME B16.5 is a widely recognized standard that outlines specifications for pipe flanges and flanged fittings, including guidelines for flange bolt dimensions, materials, and torque requirements. Adhering to ASME B16.5 ensures compatibility between components and promotes safety and reliability in high-pressure applications.
How do you tighten flange bolts?
Properly tightening flange bolts is critical to ensuring an even seal and preventing leaks. Use a calibrated torque wrench to apply the specified torque, lubricate the threads and nut faces to reduce friction, and follow a star-pattern tightening sequence to distribute clamping force evenly across the flange. Repeat the sequence in incremental steps to achieve uniform compression.
What are the different types of flange bolts?
Flange bolts come in various types, including stud bolts, hex bolts, and socket head cap screws. Stud bolts are commonly used in flanged connections, featuring threads on both ends secured with nuts. Hex bolts and socket head cap screws are often chosen for specific flange designs and operational requirements.
How do you choose the right flange bolt size?
Choosing the correct flange bolt size involves considering the flange class, pressure rating, and material requirements. Refer to ASME B16.5 or manufacturer specifications to determine the appropriate bolt diameter, length, and quantity for your specific application.
Is there a specific Flange bolt torque chart?
Torque values vary based on the bolt size, flange class, and gasket material. For example, an ASME B16.5 torque chart could provide recommended torque values for different flange sizes and materials to ensure safe and reliable connections. Accessing a detailed torque chart can help you apply the correct torque for your specific setup, reducing the risk of leaks or damage.
What is the difference between a flange bolt and a regular bolt?
Flange bolts are designed to handle the unique stresses of flange connections, often made from high-strength materials to withstand pressure, temperature, and environmental factors. Unlike regular bolts, flange bolts typically feature longer shanks and are used with specialized nuts and washers to maintain secure and leak-proof connections in critical applications.
At Component Solutions Group, we provide high-quality flange bolts and expert guidance to meet the demands of even the most challenging applications. With our wide range of solutions and commitment to precision engineering, we help you achieve secure, reliable, and efficient connections.
Contact us today to learn how CSG can support your flange bolt needs and optimize your operations.