Heavy-Duty Fasteners: Types, Applications, and Selection Criteria
- Brittany St. Clair
- Feb 7
- 10 min read
Updated: Feb 14
Disclaimer: This blog is for informational purposes and provides a general overview of heavy-duty fasteners. For specific projects, consult a qualified professional like Component Solutions Group or refer to industry standards to ensure safety and compliance.

A recent customer of ours in the transportation industry was struggling with fasteners loosening under constant vibration and load shifts. Their existing bolts were failing, leading to costly maintenance and downtime. Our team identified the issue, recommended high strength locking fasteners with a specialized coating, and helped implement a long-term solution that improved safety and reduced maintenance costs.
This experience is just one of many that highlight the critical role of heavy-duty fasteners across industries. From construction to aerospace, these essential components must withstand extreme conditions, heavy loads, and environmental challenges. In this blog, we’ll break down the different types of heavy-duty fasteners, their applications, and the key factors to consider when selecting the right one for your project—ensuring strength and reliability in every connection.
At Component Solutions Group (CSG), we know that the right fastener can make all the difference in demanding applications. Whether it's preventing vibration-induced loosening in industrial machinery or ensuring corrosion-resistant performance in offshore structures, we've worked closely with engineers, manufacturers, and project managers to provide solutions that enhance durability and reliability.
Types of Heavy-Duty Fasteners
Selecting the right type of fastener for your application is critical to ensuring the safety, reliability, and longevity of your project. Heavy-duty fasteners are designed to handle extreme loads, environmental conditions, and specialized applications. Below, we explore the most common types:
Bolts
Bolts are the cornerstone of heavy-duty fastening, offering unmatched strength and reliability. These threaded fasteners work in conjunction with nuts to secure materials together in high-stress environments. Hex bolts, for example, are widely used in construction and machinery due to their ease of installation and high tensile strength.
Carriage bolts, with their smooth, rounded heads, are ideal for applications where aesthetics and security are important, such as wooden structures or furniture. Anchor bolts, designed specifically for securing objects to concrete or masonry, are indispensable in infrastructure projects like bridges and high-rise buildings. Their ability to handle extreme loads makes bolts an essential component in industries where safety and stability are paramount.
Screws
Screws are incredibly versatile and are prized for their precision and holding power. Unlike bolts, screws can often be used without nuts, thanks to their self-threading design. Wood screws, with their sharp points and deep threads, are ideal for woodworking projects where a secure grip is necessary. Machine screws, on the other hand, are designed for metal applications and offer fine threading for tight tolerances in industrial settings. Self-drilling screws simplify installation by eliminating the need for pilot holes, making them a go-to choice for sheet metal fabrication and roofing projects. With their diverse head and drive styles, screws are the fastener of choice for applications requiring adaptability and ease of use.
Rivets
Rivets are permanent fasteners that provide unparalleled strength and durability in critical applications. Blind rivets are particularly popular in construction and automotive industries because they can be installed from one side, making them perfect for tight or hard-to-reach spaces. Solid rivets, often used in aerospace applications, are prized for their ability to withstand extreme pressures and vibrations. Tubular rivets, with their hollow shafts, are commonly used in lightweight assemblies such as electronics or furniture. The permanent nature of rivets ensures that once installed, they provide a secure, lasting bond that withstands wear and tear, even in demanding environments.
Anchors
Anchors are specialized fasteners designed to secure objects to concrete, brick, or stone. Wedge anchors, known for their exceptional holding power, are frequently used in structural applications like securing heavy machinery or foundation bolts. Sleeve anchors, which expand upon installation, provide versatility for attaching items like railings and signage to masonry surfaces. Concrete screws are a simpler option, offering the convenience of direct installation without the need for pre-installed sleeves. With their ability to handle substantial loads in challenging conditions, anchors are a cornerstone of infrastructure and heavy equipment installation.

Pins
Pins may seem simple, but their role in construction and machinery is vital. Cotter pins, for instance, are used to secure bolts or nuts in place, preventing them from loosening during operation. Dowel pins, made for precise alignment, are crucial in mechanical systems where components must fit together seamlessly. Clevis pins, often used in automotive and industrial applications, act as pivots or hinges, enabling controlled movement in complex systems. Pins are the superheroes of heavy-duty fastening, ensuring stability, alignment, and functionality across a wide range of applications.
Each of these fastener types plays a unique role in construction, manufacturing, and industrial projects. Understanding their specific features and ideal applications is the first step in ensuring the success of your project.
Applications of Heavy-Duty Fasteners
Heavy-duty fasteners are indispensable in a wide array of industries, serving as the backbone of structural integrity and functionality in critical applications. Below, we dive into the major sectors where these fasteners play a pivotal role.
Construction and Infrastructure
In construction and infrastructure projects, heavy-duty fasteners ensure stability and durability in buildings, bridges, tunnels, and other large structures. Anchor bolts are crucial for securing foundations to concrete, providing the strength needed to support towering skyscrapers and massive industrial facilities. Structural bolts connect steel beams in bridges and high-rise buildings, ensuring load-bearing capabilities and resistance to dynamic forces like wind and seismic activity. Screws and specialized fasteners attach cladding and panels, combining aesthetic appeal with long-term protection against environmental elements. Without these fasteners, the safety and longevity of modern infrastructure would be at significant risk.
Automotive and Transportation
The automotive and transportation industries rely heavily on fasteners to assemble and secure critical vehicle components. High-strength bolts are essential for chassis and suspension systems, ensuring stability and performance under dynamic loads and vibrations. Screws are used in interior components, offering precision and strength for assembling dashboards, seating, and trims. Rivets and specialty fasteners are employed in bodywork to join panels seamlessly while maintaining aerodynamic efficiency. Fasteners in this sector must meet rigorous safety and performance standards, as they are directly tied to vehicle reliability and passenger safety.
Manufacturing and Industrial Equipment
Heavy-duty fasteners are fundamental to the assembly of machinery, tools, and production lines. Bolts and screws are used extensively to secure components in industrial equipment, from conveyor belts to heavy-duty presses. Rivets join sheet metal in machinery housings, offering permanent and robust connections that withstand operational stress. In this sector, fasteners must endure high vibration, heavy loads, and repeated cycles of operation, making durability and precision paramount.
Energy and Utilities
The energy and utilities sectors demand fasteners that can perform under extreme conditions. Specialized bolts and fasteners are required in power plants, wind turbines, and oil and gas pipelines to handle high temperatures, pressures, and corrosive environments. For instance, turbine blades are secured with high-performance fasteners designed to resist thermal expansion and stress corrosion cracking. Similarly, fasteners in pipelines must ensure leak-proof connections while withstanding the challenges of chemical exposure and fluctuating pressures.
View Case Study: BUMAX Bolts Secure Wind Turbine Foundations for 27 Years
Aerospace and Defense
Aerospace and defense applications push fasteners to the limits of performance. High-performance rivets and bolts are used in airframes, providing the lightweight yet strong connections needed for flight. Specialized fasteners in engines must endure extreme heat and mechanical stress, ensuring reliability in mission-critical situations. In spacecraft and military equipment, precision-engineered fasteners are vital for maintaining operational integrity under harsh conditions, including high acceleration forces and corrosive environments.
Selection Criteria for Heavy-Duty Fasteners
Choosing the right heavy-duty fastener is critical to ensuring a project's success. Several factors influence this decision, ranging from material properties to functional requirements.
Material
The material of the fastener determines its strength, durability, and resistance to environmental factors. Stainless steel is a popular choice for its corrosion resistance, making it ideal for outdoor and coastal applications. High-strength steel is preferred for load-bearing structures and heavy-duty machinery, where tensile strength is critical. In environments with extreme temperatures or chemical exposure, superalloys like Inconel offer unmatched performance, ensuring the fastener’s longevity and reliability.
Size and Diameter
Selecting the correct size and diameter is essential to meet load requirements and ensure a secure connection. Larger diameters offer higher load-bearing capacity, making them suitable for structural applications like bridges and heavy machinery. Conversely, smaller fasteners are ideal for precision tasks, such as assembling electronic components or lightweight structures. Choosing the right size also minimizes the risk of fastener failure due to overloading or improper fit.
Read also: How to Measure Bolt Size Accurately
Thread Type
Thread type plays a significant role in the strength and locking ability of a fastener. Coarse threads are suitable for general applications where speed of installation is prioritized, while fine threads provide better tensile strength and resistance to vibration, making them ideal for precision applications. Self-tapping threads simplify installation in materials like wood or metal, eliminating the need for pre-drilled holes and speeding up assembly processes.
Head Type and Drive
The head type and drive design of a fastener determine how easily it can be installed or removed and how much torque it can handle. Hex heads are a common choice for high-torque applications, providing stability during installation. Phillips heads are versatile and widely used for general-purpose fastening. For specialized tasks, fasteners with unique drives like Torx or square drives offer improved grip and reduced slippage, ensuring secure and efficient fastening.
Coating and Finish
Coatings and finishes enhance the performance and longevity of fasteners by providing an extra layer of protection against environmental factors. Zinc plating offers basic corrosion resistance for indoor applications, while galvanized finishes are preferred for outdoor use due to their superior rust prevention. Powder coatings and advanced finishes like ceramic or nanotechnology coatings provide enhanced durability and aesthetic appeal, making them ideal for applications exposed to harsh weather or chemicals.
Common Challenges with Heavy-duty Fasteners
Heavy-duty fasteners face unique challenges that can compromise their performance and the safety of the structures they support. Issues like corrosion, vibration loosening, and fatigue failure are common, especially in demanding environments. Addressing these challenges through proper material selection, design, and installation practices is crucial for ensuring durability, reliability, and long-term success in heavy-duty applications.
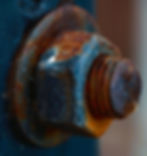
Corrosion
Corrosion is one of the most common challenges faced by fasteners exposed to harsh environments, such as coastal areas, chemical plants, or outdoor construction. Prolonged exposure to moisture, salt, and chemicals can weaken the fastener material, leading to rust and structural degradation. Corrosion not only affects the fastener’s lifespan but also risks compromising the safety and integrity of the entire structure.
Solution: Choosing corrosion-resistant materials like stainless steel or hot-dipped galvanized fasteners is essential for combating rust. In more extreme environments, advanced coatings like epoxy or ceramic can provide superior protection. Regular inspection and maintenance also help identify and address corrosion early.
Vibration Loosening
Vibration from machinery, wind, or traffic can cause fasteners to loosen over time, especially in dynamic environments like manufacturing plants, bridges, or vehicles. Loose fasteners compromise the stability and safety of the connected parts, increasing the risk of failure.
Solution: Locking fasteners, such as lock washers, nylon-insert nuts, or prevailing torque nuts, are effective in resisting loosening caused by vibration. Thread-locking adhesives and precise torque application during installation can further ensure a secure connection.
Galling and Seizing
Galling occurs when threads on fasteners bind or seize due to excessive friction during installation. This problem is especially common in stainless steel fasteners, where the material's ductility and oxidation tendencies exacerbate the issue. Galling can make installation difficult and damage both the fastener and the mating component.
Solution: Using anti-seize lubricants on threads reduces friction and prevents galling. Proper torque application with calibrated tools also ensures smooth installation without excessive force.
Fatigue Failure
Fasteners subjected to repeated loading and unloading, such as in bridges, wind turbines, or industrial machinery, can experience fatigue failure. Over time, even small cyclic stresses can cause cracks and eventual breakage, posing significant safety risks.
Solution: Fasteners with high fatigue strength, such as those made from heat-treated alloy steels, are critical for cyclic loading applications. Adhering to fatigue design principles and conducting regular inspections can help identify early signs of failure.
Stress Corrosion Cracking
In environments combining high tensile stress and corrosive agents, stress corrosion cracking (SCC) can compromise the structural integrity of fasteners. SCC typically occurs in high-strength steels and is a common concern in chemical plants or marine applications.
Solution: Selecting materials resistant to SCC, such as stainless steel or superalloys, is essential in such environments. Stress-relief annealing during manufacturing can also reduce internal stresses that contribute to SCC.
Hydrogen Embrittlement
High-strength steel fasteners used in electroplating or exposed to hydrogen environments may suffer from hydrogen embrittlement, which makes them brittle and prone to sudden failure under load.
Solution: Avoid using high-strength steel fasteners in environments where hydrogen embrittlement is a concern. Use properly processed fasteners, and ensure hydrogen diffusion treatments post-manufacture to minimize risks.
Over-Torqueing
Applying excessive torque during installation can strip threads, deform the fastener, or damage the connected materials. This often results from a lack of proper tools or over-reliance on manual judgment.
Solution: Always use calibrated torque wrenches and follow the manufacturer’s torque recommendations. Proper training for installers and adherence to standard practices also prevent over-torquing issues.
Conclusion: Strength and Reliability in Every Connection
Heavy-duty fasteners are more than just functional components; they are the unsung heroes that ensure the strength, safety, and durability of critical projects. From construction and manufacturing to energy and aerospace, these fasteners must meet the challenges of corrosion, vibration, fatigue, and environmental stresses head-on. By understanding the common pain points and employing the right materials, coatings, and designs, you can achieve connections that stand the test of time.
At Component Solutions Group (CSG), we specialize in precision-engineered fasteners designed to excel under the toughest conditions. Whether you need corrosion-resistant materials, vibration-resistant locking mechanisms, or customized solutions for unique challenges, CSG is your trusted partner for heavy-duty fastening solutions. Reach out to us today to explore how we can enhance your projects with unparalleled strength and reliability.
Frequently Asked Questions (FAQs)
What are the different grades of heavy-duty fasteners?
Heavy-duty fasteners are classified by grading systems such as SAE, ASTM, and metric grades. These grades denote tensile strength, yield strength, and durability, with higher grades designed for demanding applications like structural or load-bearing connections.
How do I choose the right heavy-duty fastener for my application?
To choose the right fastener, consider load requirements (tensile and shear forces), environmental factors (corrosion, temperature), material compatibility, and specific features like thread type and head design. Proper selection ensures strength, durability, and secure connections.
What are the most common materials used for heavy-duty fasteners?
Popular materials include carbon steel for affordability and strength, alloy steel for enhanced performance, stainless steel for corrosion resistance, and superalloys for extreme conditions like high temperatures or chemical exposure.
What are the latest advancements in heavy-duty fastener technology?
Recent innovations include lightweight materials that maintain strength, advanced coatings for superior corrosion resistance, smart fasteners with sensors to monitor tension, and 3D-printed fasteners tailored for unique applications.
How do I prevent heavy-duty fasteners from loosening due to vibration?
Prevent loosening by using lock washers, thread-locking adhesives, or prevailing torque nuts. Apply the correct torque during installation and conduct regular inspections to ensure secure and stable connections.