Innovative Fastening Solutions for Composite Materials
- Brittany St. Clair
- Jul 19, 2024
- 4 min read
Custom Solutions in Plastic, Fiberglass, and Aluminum Assemblies
The Engineered Fastening Systems Division of CSG, backed by a team of seasoned experts, is taking its parent company’s name literally. “We want engineering teams to understand that we are a complete component solution,” says Sales Engineer and Business Development Representative Chris Seidell. We’re working side-by-side with engineers across all industries to provide complete fastened joint solutions.”
CSG’s customers know that working with a single solutions partner makes the design, prototyping, and testing process easier and more cost-effective. This is especially true since each joint can be customized for the specific project and its unique requirements, which could involve multiple vendors to make each part. This would include specially designed blind fasteners and compression limiters to address the challenges of working with the variety of composite materials in use today.

CSG offers many solutions for applications where strength and corrosion resistance are essential. A recent aerospace challenge involved connecting a windscreen to a composite structure on a military heavy-lift helicopter. The base of the graphite/carbon epoxy composite structure varies in thickness from .125” to .500”. The customer needed a fastener that was strong enough to hold on the windscreen, resist corrosion, and prevent rotation built into the part. The solution developed was the “Teardrop” rivet nut fastener.
It is a stainless steel, thread-locked, dry film-lubricated, special head configuration Rivetnut. The stainless material provides corrosion resistance, the dry film lube prevents thread damage when using stainless bolts into a stainless nut (galling), and the special head configuration in the form of a “teardrop” allows the OEM to add a satellite rivet hole to tack down the rivet nut head and prevent torque (spin) out.
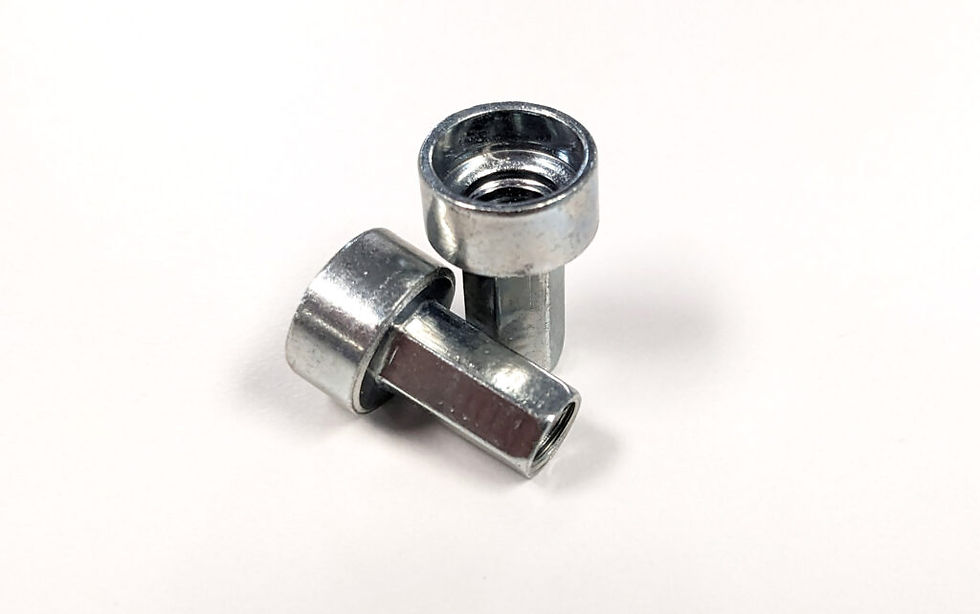
“One issue that became apparent immediately was that the composite manufacturers couldn’t use hex holes, which is the best practice for rivet nuts to prevent spin-out. Since composite material cannot be punched the way that sheet metal can be, it was imperative the CSG team came up with a part that met the torque requirements but didn’t damage the mating material while still being corrosion-resistant. “We’ve found that our solutions are especially effective when customers have to attach components to fiberglass and other plastics, so getting this expertise into the hands of our customers' engineers has been a primary objective of our sales teams,” says Dennis, General Manager, Engineered Fastening Systems Division of CSG.
Another solution developed to address these issues is the Optisert Round Body Rivet Nut, designed and manufactured by an esteemed fastener solutions provider. This specialized part features aggressive wedges under the head, which press into the parent material to increase resistance to spin-out significantly. This enhancement provides an even stronger thread in softer materials like plastic, fiberglass, and aluminum. Since the Optisert meets Class 8 and Grade 5 thread-proof loads, the CSG team has been able to design it into a multitude of applications. The wider head of this part also helps distribute the installation stress over a greater area, reducing the potential for parent material damage. "We have been extremely proud to be an authorized distributor for over 15 years and are excited about this new Optisert product," adds Dennis. "We pride ourselves on offering sustainable and innovative solutions, so having partners like this is essential for our design team."
For example, we’ve worked with several OEMs on attaching components to Rotomolded plastic materials. Rotomolded products are notorious for having very wide tolerances. For instance, one side of a rotomolded part can be .125”, and the other side of the same part (say 1 foot away) may be 0.205. Our Slotted or Plusnut product has a wide grip range (.250”), allowing the OEM to use the same part in various thicknesses that arise due to the molding process.”
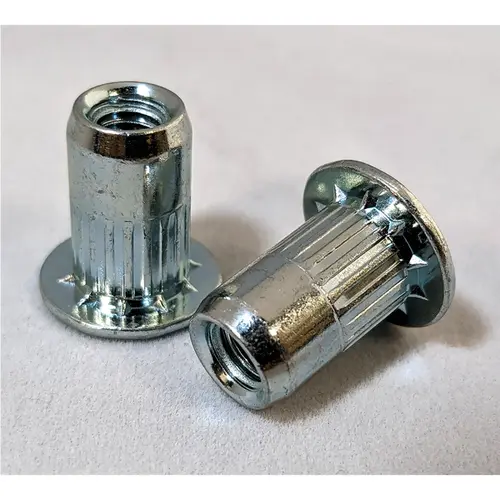
Other applications, however, require the use of compression limiters. This concept has continued to evolve as engineers find ways to build them into the rivet nut or design them as a separate element to prevent parent material compression and damage.
Design variations like this can significantly add value to the joint design and assembly process. Compression limiters can be customized and manufactured according to the customer's specifications.
"Our team has a long history working to identify and solve challenges unique to the OEM’s assembly of composites.“ –Dennis Edwards, General Manager.
The CSG team is not only focused on helping engineering teams design, develop, and manufacture unique designs, but also on pushing the boundaries of what's possible in the industry. This is where the total cost of ownership starts to really add up. Engineers and sourcing teams need to be able to evaluate and design parts for the life cycle of a given component and its assembly. Sometimes, having the least expensive option can prove to cost more in the long term, so doing the needs analysis correctly and accurately at the very beginning is important.
About The Engineered Fastening Systems Division of CSG
The Engineered Fastening Systems Division of CSG is at the forefront of innovative fastening solutions, specializing in the design and development of high-performance fasteners for composite materials. Our commitment to excellence drives us to continuously push the boundaries of what is possible in engineered fastening systems. From the initial design phase to prototyping and testing, we work closely with engineering teams across various industries to ensure the highest quality and performance.
CSG's Engineered Fastening Systems Division will be at the CamX show in San Diego from September 9 to 12. Visit booth K39 to view models of some of our recent design solutions!
Contact our team of experts today to learn more about CSG's fastening systems or any of our component solutions and discover how we can take your business and engineering capabilities to the next level.