7 Proven Workflow Optimization Strategies for OEM Manufacturers
- Brittany St. Clair
- 5 days ago
- 4 min read
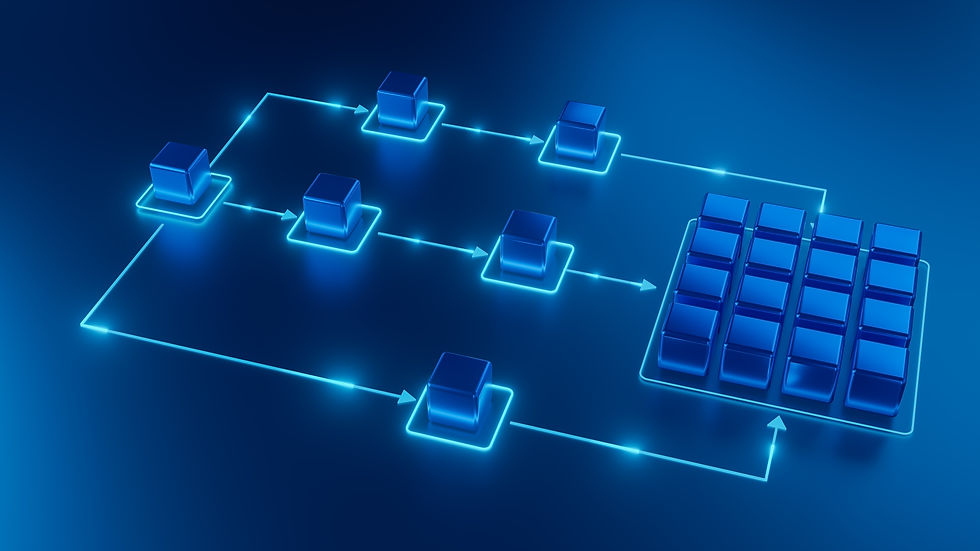
From RFQs to custom part production to delivery under tight deadlines, we’ve seen firsthand how broken workflows stall efficiency—and we’ve helped our partners fix them. If you're an engineer or C-parts purchasing agent dealing with bottlenecks, rework loops, or inconsistent outputs, this guide is for you.
This article outlines proven, tactical steps OEMs can take to optimize production workflows, reduce waste, and deliver better results—without reinventing the wheel.
Why Workflow Optimization Matters for OEM Manufacturers
OEM environments are uniquely demanding. You're balancing strict customer specs, part number traceability, quality compliance (ISO 9001, IATF 16949), and supply chain coordination across multiple vendors. One breakdown in your workflow—and suddenly, delivery timelines are at risk.
By optimizing your production workflows, you can:
Improve delivery performance
Reduce lead times and overhead
Eliminate redundant or manual steps
Free up capacity to scale
Workflow optimization isn't just an operations initiative—it’s a competitive differentiator.
Step 1: Map Your OEM Workflows
Start by visually mapping out your current workflows, from customer order entry through engineering review, scheduling, procurement, fabrication, inspection, and delivery.
Use tools like flowcharts or process diagrams to clarify every step, including:
Engineering Change Orders (ECOs)
Material requisitions
First Article Inspection (FAI) loops
Subcontracted operations
Clarity here uncovers hidden redundancies and sets the stage for improvement.
Step 2: Track the Right KPIs
Data-driven decisions are key. Identify and monitor the most relevant production metrics for your operation:
Cycle Time – How long does it take to complete a production run from start to finish?
Throughput – Total number of units produced in a given time period
Scrap & Rework Rates – Especially critical for tight-tolerance or regulated parts
On-Time Delivery (OTD) – A direct reflection of process efficiency
Industry Insight: A study by Hewlett-Packard's Vancouver division reported a reduction in throughput time from 17 days to 30 hours after implementing lean practices.
Compare internal benchmarks against industry standards to identify where improvement is needed most.
Step 3: Use the 7-Step Process Improvement Model
OEMs benefit from a structured approach to fixing broken workflows. Here’s a practical breakdown:
Define – Pinpoint the specific process issue.
Measure – Collect data to understand the scope and impact.
Analyze – Identify root causes using tools like fishbone diagrams or Pareto charts.
Improve – Test potential solutions through pilots or Kaizen events.
Control – Implement process controls and SOPs to standardize the improvement.
Review – Reassess the process periodically to catch slippage.
Document – Maintain version-controlled documentation for reference and training.
Step 4: Leverage Frontline Knowledge
Shop floor employees and line operators often see inefficiencies that leadership doesn’t. Encourage cross-functional input during workflow reviews. Their real-world feedback can uncover:
Setup inefficiencies
Communication delays
Redundant documentation steps
Engaging these voices builds ownership and results in more sustainable improvements.
Step 5: Apply Lean Manufacturing Principles
Lean isn’t just for high-volume OEMs. Even low-to-mid volume manufacturers can benefit from:
5S – Keep the work environment organized and visual
Just-in-Time (JIT) – Minimize inventory waste and improve flow
Value Stream Mapping – Identify non-value-added steps across processes
Standard Work – Ensure consistency across shifts and operators
Case Study: Daman Products achieved a 97% reduction in cycle times and a 50% reduction in setup times by implementing lean-focused cellular factories and pull scheduling.
When implemented properly, Lean helps you do more with less—without compromising quality.
Step 6: Embrace the Right Technology
Tech can enhance—but not replace—good processes. Prioritize tools that support visibility, traceability, and real-time performance monitoring:
ERP & MES Software – Unify scheduling, inventory, work instructions, and job tracking
IoT Sensors – Monitor machine performance, downtime, and predictive maintenance
Automation – Reduce human error and speed up repetitive operations
Ensure new tech integrates with your existing systems to avoid creating silos.

Step 7: Monitor, Adjust, and Improve Continuously
After implementing changes, set up a cadence to monitor outcomes. Use dashboards and team huddles to:
Review performance against KPIs
Identify new bottlenecks
Adjust processes or retrain teams as needed
Continuous improvement should be embedded in your company culture—not treated as a one-time event.
CSG's Approach to Smarter Workflows
At Component Solutions Group (CSG), we’ve helped OEMs reduce lead times, streamline order management, and eliminate costly production loops by improving the systems behind the parts. Whether you're retooling a process for a new product line or trying to hit tighter delivery windows, we’re here to help you rethink how workflows.
Let’s Talk Workflow
If your current processes feel disconnected, redundant, or outdated, you’re not alone—and you’re not stuck. Let’s explore how CSG can support your workflow optimization goals, from strategic planning to real-world implementation.
👉 Contact us to start a conversation with our manufacturing systems team, or request a consult to see where we can help streamline your next project.
Disclaimer: The information provided in this article is based on industry best practices and publicly available sources. While we’ve made every effort to ensure accuracy and relevance, each OEM operation is unique. For guidance specific to your components, systems, or compliance requirements, please consult with an experienced manufacturing partner like CSG. We’re here to help you apply the right solutions for your workflow, supply chain, and production goals.