Rail and Bridge Fasteners: Securing Critical Infrastructure
- Brittany St. Clair
- Feb 18
- 12 min read
Disclaimer: We have made every effort to provide accurate and detailed information in this blog to offer insights into the role and importance of rail and bridge fasteners in infrastructure projects. However, each situation is unique, and it is essential to consult a certified professional for specific engineering requirements. Always refer to applicable industry standards and regulations to ensure compliance and optimal performance.
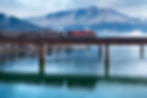
A long-time railway customer came to Component Solutions Group (CSG) with a critical issue—fastener failures on a busy freight line were causing costly delays and safety concerns. Despite using standard fasteners, constant vibration, heavy loads, and harsh weather led to premature wear and track misalignment.
After analyzing their environment, CSG engineered a custom fastening solution—high-strength bolts with advanced corrosion resistance and a locking mechanism to prevent loosening. The result? A 60% reduction in maintenance costs and improved track stability.
This challenge isn’t unique. Across railway and bridge infrastructure, fasteners keep everything securely in place, bearing immense loads and resisting environmental stressors for decades. However, selecting the wrong fasteners or neglecting proper maintenance can lead to costly failures and serious safety risks.
From rail clips absorbing constant vibrations to anchor bolts securing massive bridge structures, each component plays a critical role in infrastructure longevity. In this blog, we’ll break down the key types of fasteners used in rail and bridge construction, the materials that maximize durability, and the best practices for maintenance and inspection—ensuring infrastructure that stands the test of time.
Types of Rail Fasteners: Securing Rail Infrastructure with Precision
Rail fasteners are the backbone of track systems, ensuring stability, alignment, and safety under demanding conditions. From rail clips that absorb vibrations to bolts and nuts that provide high-strength connections, each type plays a critical role in maintaining efficient and reliable rail operations.
Rail Clips: The Guardians of Track Stability
The global demand for rail clips continues to grow, driven by investments in rail infrastructure and urban transit projects. With the market valued at $2.1 billion in 2022 and projected to grow at a compound annual growth rate (CAGR) of 4.2% through 2030, innovations in clip materials and designs are further enhancing their performance and longevity.
Rail Anchors: Preventing Rail Creep and Ensuring Safety
Rail anchors play a critical role in maintaining the track gauge by preventing longitudinal movement of the rails. This is particularly important in areas with heavy train traffic or significant temperature fluctuations, which can cause rail creep. By securing the rails in place, rail anchors not only maintain operational safety but also reduce wear on other track components, such as ties and clips.
Advanced rail anchor designs have made these fasteners more efficient, enabling better performance with fewer components. Properly installed rail anchors can reduce track maintenance costs by up to 20%, as highlighted in a study published in the Journal of Rail and Rapid Transit. This makes them a cost-effective solution for maintaining rail infrastructure while ensuring passenger and freight safety.
Rail Spikes: A Classic Reinvented
Rail spikes have been a cornerstone of rail construction since the early days of the industry. Their distinctive design, featuring a pointed end and a flat head, allows them to secure rails to ties effectively. Although traditionally made from iron, modern rail spikes are now manufactured from high-strength steel and often feature protective coatings to enhance durability and resist corrosion.
With over 1 billion rail spikes in use across North America, their importance in maintaining track stability cannot be overstated. Newer designs and materials have improved their performance, making them suitable for high-stress applications, including heavy freight and high-speed rail systems. Rail spikes remain a cost-effective solution for securing rails in both traditional and modern track systems.
Bolts and Nuts: The Backbone of Rail Joints
High-strength bolts and nuts are essential for connecting rail joints and fastening systems, particularly in areas where structural integrity is paramount. These fasteners provide exceptional tensile strength and durability, ensuring that rail segments remain securely connected under heavy loads and high stress. Their versatility allows them to be used in various rail configurations, including continuous welded rail (CWR) and jointed track systems.
As rail infrastructure expands globally, the demand for reliable bolts and nuts is surging. The railway fasteners market, which includes these components, is projected to reach $10.5 billion by 2027, driven by increasing investments in rail safety and efficiency. Advanced manufacturing techniques and materials have further enhanced the performance of these critical fasteners, ensuring they meet the rigorous demands of modern rail systems.
Bridge Fasteners: Strengthening Critical Infrastructure
Bridge fasteners are essential components in maintaining the structural integrity and safety of bridges, bearing immense loads and withstanding environmental stressors. These specialized fasteners ensure that every component, from girders to foundations, remains securely connected to handle the dynamic forces bridges endure daily.
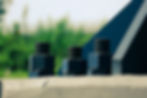
Anchor Bolts
Anchor bolts play a pivotal role in connecting bridge components to their foundations. These fasteners are designed to bear significant loads and resist movement caused by environmental factors like wind, seismic activity, and heavy traffic. By firmly securing structural elements to the foundation, anchor bolts provide stability and prevent failures in critical areas. They are a cornerstone of bridge safety, ensuring long-term reliability and performance.
Tension Control Bolts (TCBs)
Tension control bolts are a modern solution for achieving precise preloads in bridge construction. Their design allows for easy installation while maintaining consistent tension across structural connections. TCBs improve structural integrity, ensuring that load-bearing components, such as beams and joints, remain secure. Their efficiency in installation also makes them a time-saving choice in large-scale bridge projects, reducing construction timelines without compromising safety.
High-Strength Structural Bolts
High-strength structural bolts are engineered to withstand the immense stress and forces bridges encounter. Used in connecting girders, beams, and other load-bearing components, these bolts provide exceptional tensile and shear strength. Their reliability ensures that even under heavy traffic and environmental fluctuations, bridges maintain their structural integrity, making them indispensable in modern bridge construction.
Customized Fasteners
Customized fasteners address unique challenges in bridge design, offering tailored solutions for unconventional configurations or specialized requirements. Whether it’s a fastener designed to withstand extreme temperatures or one that integrates seamlessly into unique architectural elements, customized options ensure that every bridge design achieves its intended performance and aesthetic goals.
Materials Used in Rail and Bridge Fasteners
The performance of rail and bridge fasteners heavily depends on the materials used in their construction. The right materials ensure durability, resistance to environmental factors, and the ability to withstand extreme loads and stresses. From traditional metals to advanced composites, these materials are engineered to meet the evolving demands of critical infrastructure.
Steel
Steel remains the most widely used material for rail and bridge fasteners due to its exceptional strength and versatility. Different grades of steel, such as high-carbon steel and alloy steel, offer varying levels of tensile strength, ductility, and corrosion resistance. High-carbon steel is ideal for applications requiring strength and durability, while alloy steels provide enhanced performance under extreme conditions. Steel fasteners are essential for heavy-duty applications where long-term reliability is critical, especially in high-stress environments like bridge joints and rail systems.
Iron
Historically, iron was a foundational material for fasteners used in rail and bridge construction due to its abundance and ease of manufacturing. It was particularly valued in earlier infrastructure projects where strength requirements were moderate, and cost-efficiency was paramount. However, iron’s inherent limitations, such as vulnerability to rust and lower tensile strength compared to modern alloys, have diminished its role in critical applications. Today, iron is largely used in traditional or ornamental projects, where its aesthetic appeal or historical authenticity is prioritized over its performance. Advances in steel and composite materials have largely supplanted iron for most structural uses.
Composites
Composite materials, such as fiber-reinforced polymers, are gaining traction in the fastener industry for specialized applications. Lightweight yet strong, composites offer exceptional corrosion resistance, making them ideal for environments exposed to moisture, chemicals, or extreme weather conditions. Their non-conductive properties also make them suitable for use in areas with electrical or magnetic interference, such as rail signaling systems. As technology evolves, composites are expected to play a larger role in infrastructure projects requiring innovative materials.
Coatings and Platings
Protective coatings and platings are crucial for enhancing the longevity and performance of fasteners. Galvanization, zinc plating, and powder coatings provide an additional layer of protection against corrosion, ensuring that fasteners maintain their integrity even in harsh conditions. These treatments are especially important in coastal and industrial environments, where exposure to salt, pollutants, and chemicals can accelerate degradation. Coated fasteners not only extend the lifespan of infrastructure but also reduce long-term maintenance costs.
Importance of Quality and Standards
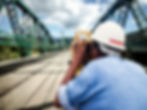
The reliability of rail and bridge fasteners directly impacts the safety and longevity of critical infrastructure. Quality and adherence to industry standards are paramount to ensure fasteners perform under extreme conditions without failure. From production to installation, a rigorous focus on standards, testing, and traceability ensures fasteners meet the stringent demands of modern engineering.
Industry Standards
Industry standards, such as ASTM and ISO, provide clear guidelines on material properties, manufacturing processes, and performance criteria for rail and bridge fasteners. These standards ensure that fasteners are engineered to meet specific requirements for strength, durability, and safety. Compliance with these standards fosters consistency across projects and minimizes the risk of failure. For instance, ASTM standards for tensile strength and ISO certifications for quality management systems help maintain a benchmark of excellence across the industry.
Testing and Certification
Fasteners used in critical infrastructure must undergo comprehensive testing to ensure they meet performance requirements. Common tests include tensile strength assessments to measure a fastener’s load capacity, fatigue testing to evaluate long-term durability, and corrosion resistance evaluations. Certifications from recognized bodies, such as ISO or national testing laboratories, validate that fasteners meet industry and project-specific criteria. These certifications not only ensure safety but also build trust in the quality of the components.
Traceability
Traceability in fastener manufacturing allows for complete accountability and quality control throughout the production and supply chain. Each fastener is marked with unique identifiers or batch numbers, enabling engineers to trace it back to its origin, materials used, and quality checks performed. This practice is crucial for addressing potential defects or failures, ensuring a swift response, and maintaining the integrity of the entire project.
Maintenance and Inspection
Maintaining the integrity of rail and bridge fasteners is vital for ensuring the ongoing safety and performance of infrastructure. Regular maintenance and inspections help identify potential issues before they escalate, extending the lifespan of the structure and reducing the need for costly repairs.
Visual Inspection
Regular visual inspections are the first line of defense in identifying wear, damage, or corrosion in fasteners. Engineers can quickly spot issues such as surface rust, cracks, or misalignment that may compromise performance. These inspections are particularly important in environments with high exposure to moisture, salt, or pollutants.
Non-Destructive Testing (NDT)
NDT methods, such as ultrasonic testing and magnetic particle inspection, allow for the detection of hidden flaws in fasteners without causing damage. These advanced techniques can identify internal cracks, voids, or material weaknesses that may not be visible during a routine inspection, ensuring a more thorough evaluation of fastener integrity.
Torque Wrenching
Proper torque wrenching during installation and maintenance ensures that fasteners achieve optimal clamping force. Incorrect torque application can lead to loosening, overloading, or thread damage, compromising the connection. Using calibrated torque wrenches and adhering to recommended specifications helps maintain structural stability.
Replacement Schedules
Fasteners have a defined service life based on material properties and environmental exposure. Following recommended replacement schedules ensures that worn or degraded fasteners are replaced before they fail. Regular maintenance logs and monitoring systems help track the condition of fasteners and ensure timely replacements, preventing unexpected failures.
Challenges and Solutions in Rail and Bridge Fastener Applications
Fasteners in rail and bridge construction encounter numerous challenges due to the demanding environments and operational stresses they face. Addressing these challenges is critical to ensuring long-term structural integrity and operational safety. Below, we discuss key issues and their corresponding solutions.

Corrosion
Corrosion remains one of the most significant challenges for fasteners in rail and bridge applications, particularly in coastal areas, industrial zones, or regions with high humidity. Constant exposure to moisture, salt spray, and industrial chemicals accelerates rust formation and weakens the fasteners. Over time, this can lead to structural instability and costly repairs. Bridges, in particular, are vulnerable to corrosion due to their exposure to varying weather conditions and pollutants.
To combat corrosion, materials like stainless steel and hot-dipped galvanized fasteners are commonly used. These materials resist rust and degradation, ensuring the longevity of the fasteners. Advanced protective coatings, such as zinc plating or ceramic finishes, provide an additional barrier against environmental wear. Regular maintenance and inspections also play a crucial role in identifying early signs of corrosion and replacing affected fasteners before they compromise structural safety.
Vibration and Fatigue
Dynamic loads caused by train movements, wind, and heavy traffic induce constant vibrations and stress cycles on fasteners. Over time, this repetitive loading can loosen fasteners or lead to fatigue failure, particularly in critical structural elements like bridge joints and rail connections. Loose fasteners increase the risk of structural instability and require frequent maintenance to avoid catastrophic failures.
Using vibration-resistant fasteners, such as those with lock washers or nylon-insert nuts, is an effective strategy to mitigate this issue. Thread-locking adhesives also provide additional security by preventing loosening over time. For applications subjected to high stress, fasteners made from fatigue-resistant alloys are essential. Regular torque inspections and re-tightening schedules can further ensure that fasteners remain secure under dynamic loads.
Thermal Expansion and Contraction
Temperature fluctuations cause materials to expand and contract at different rates, putting additional stress on fasteners. In rail tracks and bridge connections, this phenomenon can lead to loosening or misalignment, particularly in regions with extreme seasonal variations. Over time, these temperature-induced stresses can weaken joints and reduce the structural integrity of the entire system.
Specialized fasteners designed to accommodate thermal movement, such as expansion bolts or flexible connections, are widely used in these applications. Additionally, incorporating expansion joints into the structure allows for controlled movement and reduces stress on fasteners. Engineering teams also consider material compatibility during design to ensure that fasteners and substrates expand at similar rates, minimizing the risk of damage.
Accessibility and Installation
Many fasteners in rail and bridge systems are located in hard-to-reach areas, such as beneath rail tracks or within bridge girders. This limited accessibility complicates both installation and routine maintenance. Improperly installed or poorly maintained fasteners can compromise the performance of the structure, leading to increased repair costs and safety risks.
To address these challenges, specialized installation tools, such as angled torque wrenches and compact impact drivers, are used to ensure proper fastening in tight spaces. Automated and robotic systems are also being adopted for installing and inspecting fasteners in difficult locations. Proper training for installation teams and adherence to detailed guidelines help ensure that all fasteners are installed correctly and function optimally.
Future Trends in Rail and Bridge Fasteners
As infrastructure demands grow, the fastener industry is innovating to meet evolving challenges. Emerging trends promise enhanced durability, safety, and efficiency in rail and bridge construction.
Advanced Materials
The use of advanced materials like high-strength alloys and composites is revolutionizing fasteners. These materials offer superior strength, reduced weight, and enhanced corrosion resistance, making them ideal for modern infrastructure projects.
Smart Fasteners
Smart fasteners equipped with embedded sensors are changing the way maintenance is conducted. These fasteners can monitor tension, detect early signs of stress or corrosion, and predict maintenance needs, enabling proactive infrastructure management.
Robotics and Automation
Robotic systems and automated tools are transforming fastener installation and inspection processes. These technologies improve precision, reduce labor costs, and enhance safety in complex and large-scale construction projects.
Securing the Future of Infrastructure with Reliable Fasteners
Rail and bridge fasteners are more than just components—they are the foundation of safety, stability, and longevity for critical infrastructure. Tackling challenges such as corrosion, vibration, and thermal expansion requires not only the right materials and designs but also a forward-thinking approach that embraces innovation. By leveraging advanced materials, smart technologies, and robust quality standards, the industry can ensure that railways and bridges remain safe and efficient for generations to come.
At Component Solutions Group (CSG), we don’t just provide fasteners; we deliver solutions. With precision-engineered products tailored to your unique needs, we empower your projects to meet the highest standards of reliability and performance. Partner with us to ensure your infrastructure is built to last—contact CSG today and let us help secure your success.
Frequently Asked Questions (FAQs)
What are the most common types of rail fasteners?
Rail fasteners come in various types, each serving a specific function. Rail clips secure rails to ties and absorb vibrations, while rail anchors prevent track movement. Rail spikes are traditional fasteners for securing rails to wooden or concrete ties, and bolts and nuts provide strength for joints and specialized connections. Each plays a vital role in maintaining track alignment and stability.
How do I choose the right rail fasteners for my project?
Selecting the right rail fastener involves assessing several factors, such as the type of rail and track gauge, load-bearing requirements, and environmental conditions like moisture or temperature extremes. It's also essential to adhere to industry standards and consult with experts to ensure fasteners are compatible with your infrastructure's specific needs.
What are the key maintenance practices for rail fasteners?
Regular maintenance of rail fasteners includes visual inspections for wear and corrosion, using non-destructive testing (NDT) techniques to detect hidden flaws, and applying proper torque wrenching during reinstallation. Following replacement schedules based on the fasteners’ service life and environmental exposure ensures safety and longevity.
What are the latest advancements in rail fastener technology?
Rail fastener technology has advanced with innovations like smart fasteners embedded with sensors to monitor structural health. The adoption of advanced materials, such as composites and high-strength alloys, enhances durability and corrosion resistance. Robotics and automation now streamline the installation and inspection processes, improving safety and efficiency.
How do rail fasteners impact track safety?
Rail fasteners are critical for maintaining track safety by ensuring proper alignment, stability, and load distribution. High-quality fasteners prevent rail movement, reduce derailment risks, and withstand environmental and operational stresses. Proper selection, installation, and maintenance are key to ensuring the safety of both passengers and freight.