Sustainable C-Parts: How to Master C-Part Sustainability
- Brittany St. Clair
- Feb 13
- 7 min read

Image this scenario. You’re a lead engineer at a manufacturing company, and a new sustainability audit just landed on your desk. Your company has already made big strides—investing in energy-efficient machinery, optimizing material usage, and improving waste management. But as you scan the report, something unexpected stands out: the environmental impact of your C-parts.
Fasteners, washers, and small connectors—components that seem minor in day-to-day operations—are actually creating a significant carbon footprint. They’re sourced from multiple suppliers, often shipped inefficiently across long distances, and made from non-recycled materials. The sheer volume of these tiny parts adds up fast, leading to unnecessary emissions, excess packaging waste, and procurement inefficiencies.
Now, imagine uncovering a solution that not only reduces your company’s carbon footprint but also cuts costs. By consolidating suppliers, sourcing C-parts made from sustainable materials, and optimizing logistics, you find that supply chain emissions could drop by up to 20%—all while streamlining operations and reducing procurement expenses.
At Component Solutions Group (CSG), we see this scenario play out with our customers all the time. Many manufacturers don’t initially consider the sustainability impact of their C-parts, but once they do, they realize it’s a game-changer. These small components may not always be the focal point, but their role in sustainability and cost reduction is undeniable.
Just like the companies we work with, you have the opportunity to make a difference—starting with the smallest parts in your supply chain.
Introduction: The Overlooked Role of C-Parts in Sustainability
While sustainability initiatives often focus on large components (A- and B-parts), a critical piece of the puzzle is frequently overlooked: C-parts. These small but essential components, like fasteners and washers, are used in billions of units annually across industries, and their collective impact on carbon emissions and resource consumption is substantial. This article explores the challenges and offers actionable strategies for integrating sustainable C-parts into your supply chain.
Though individually small, the sheer volume of C-parts used in manufacturing presents a significant opportunity for businesses to enhance sustainability and reduce costs. According to a 2023 report, approximately 60% of manufacturing emissions originate from supply chain operations. While C-parts are only a fraction of that total, their lifecycle—spanning raw material extraction, production, transportation, and disposal—still contributes meaningfully to environmental impact.
With regulatory frameworks like the EU Corporate Sustainability Reporting Directive (CSRD) and rising expectations from investors and consumers, businesses can no longer afford to overlook the sustainability implications of C-parts.
How C-Part Suppliers Can Help Reduce Emissions
Many manufacturers lack direct visibility into their C-part suppliers’ sustainability practices. However, partnering with sustainability-focused suppliers can significantly reduce emissions and align businesses with compliance requirements.
Key strategies for reducing C-part emissions include:
Choosing suppliers that use renewable energy in manufacturing facilities.
Sourcing C-parts made from recycled materials to minimize resource extraction.
Optimizing logistics by consolidating shipments, using fuel-efficient transportation, and strategic warehouse placement—potentially reducing transportation costs by up to 15% and lowering carbon emissions by 10-20%.
Using data-driven procurement models to forecast demand, prevent over-ordering, and reduce waste.
A 2023 study by McKinsey found that companies prioritizing emissions-conscious sourcing reduced supply chain emissions by 20% on average, saving businesses an estimated $15 million annually in logistics costs.
Making Emissions Reporting Easier
While the strategies outlined above can significantly reduce C-part emissions, they also contribute to easier emissions reporting. By partnering with sustainable suppliers, leveraging certifications, and utilizing AI-driven procurement tools, businesses can gain better visibility into their C-part supply chains. This makes Scope 3 emissions tracking and reporting a more manageable process, providing the data needed to meet regulatory requirements and demonstrate environmental responsibility.
Strengthening Supplier Collaboration
To maximize sustainability impact, businesses should consider forming strategic partnerships with C-part suppliers rather than engaging in purely transactional relationships. By actively collaborating with suppliers and setting clear sustainability expectations, businesses can drive positive change within their supply chains and ensure that their C-parts are sourced responsibly. Sustainable suppliers often adhere to globally recognized certifications, such as:
ISO 14001: Environmental management systems certification.
LEED Certification: Recognizing sustainable sourcing and supply chain practices.
EcoVadis Sustainability Ratings: Providing transparency into supplier sustainability performance.
This proactive approach to supplier engagement not only helps improve the sustainability of current suppliers but also empowers businesses to make informed decisions about future partnerships. By prioritizing suppliers with strong environmental commitments and actively collaborating on sustainability initiatives, companies can create a more resilient and responsible C-part supply chain.
Design for Sustainability: Building Greener Products from the Start
Integrating sustainable C-parts starts at the design phase. Manufacturers can minimize waste, optimize resource use, and facilitate recycling by considering material choices, component standardization, and product lifecycle from the outset.
Key design strategies include:
Reducing material variety: Using fewer types of fasteners simplifies disassembly and recycling processes.
Modular product design: Enables easy replacement of individual components, extending product lifespan and reducing the need for full replacements.
Designing for recyclability: Selecting materials with established recycling streams (such as certain grades of aluminum or steel) and avoiding complex material combinations (like plastic-coated metals) to facilitate proper sorting and processing at end-of-life.
Standardization of components: Using the same size and type of fastener across multiple product lines simplifies disassembly and sorting.
Clear material labeling: Implementing standardized recycling codes to facilitate proper recycling and material recovery.
By embedding sustainability into product design, companies can significantly cut environmental impact while improving long-term cost efficiency.
AI-Driven Procurement for Sustainable C-Parts

AI-driven procurement tools are revolutionizing the way businesses manage sustainable sourcing. Benefits include:
Optimized inventory management, reducing overordering and excess waste.
Predictive analytics, helping businesses forecast demand for recycled and eco-friendly materials.
Supplier performance tracking, identifying vendors with the strongest sustainability records.
Smart logistics planning, optimizing shipping routes and consolidating orders to minimize transportation emissions.
Tracking material sustainability, ensuring businesses prioritize recycled or bio-based options with the lowest carbon footprint.
Supplier selection based on sustainability criteria, leveraging AI to analyze certifications, emissions data, and other key environmental metrics.
Cost savings through automation, reducing procurement costs by streamlining supplier selection and minimizing inefficiencies.
AI-driven procurement tools can also help businesses optimize inventory management and logistics, avoiding the sustainability pitfalls associated with stockouts, rush orders, and inefficient transportation. By streamlining these processes, companies can minimize waste, reduce unnecessary shipments, and ensure a more sustainable C-part supply chain.
Addressing Challenges in Sustainable C-Part Adoption
Challenge: Higher Upfront Costs
Solution: While sustainable materials may have a higher initial cost, long-term benefits include reduced waste disposal fees (which can be as high as $200 per ton), regulatory compliance savings, and enhanced brand reputation. Partnering with suppliers offering volume discounts or long-term contracts can help mitigate costs.
Challenge: Ensuring Quality and Performance
Solution: Advances in material science and rigorous testing ensure that sustainable C-parts meet industry performance standards. Reputable suppliers provide certifications, specifications, and performance data to validate product reliability.
Challenge: Availability of Sustainable C-Parts
Solution: The market for sustainable C-parts is growing rapidly, though the availability of specific types of recycled or bio-based C-parts may vary depending on size, material, and application. Partnering with a specialized distributor can help businesses navigate the current market landscape and access available resources while also staying informed about emerging sustainable alternatives.
Challenge: Tracking Sustainability Across the Supply Chain
Solution: Emerging technologies such as blockchain and digital tracking systems provide greater transparency in C-part supply chains. These tools help businesses verify the origin, sustainability credentials, and carbon footprint of their C-parts.
Real-World Sustainability Success Stories
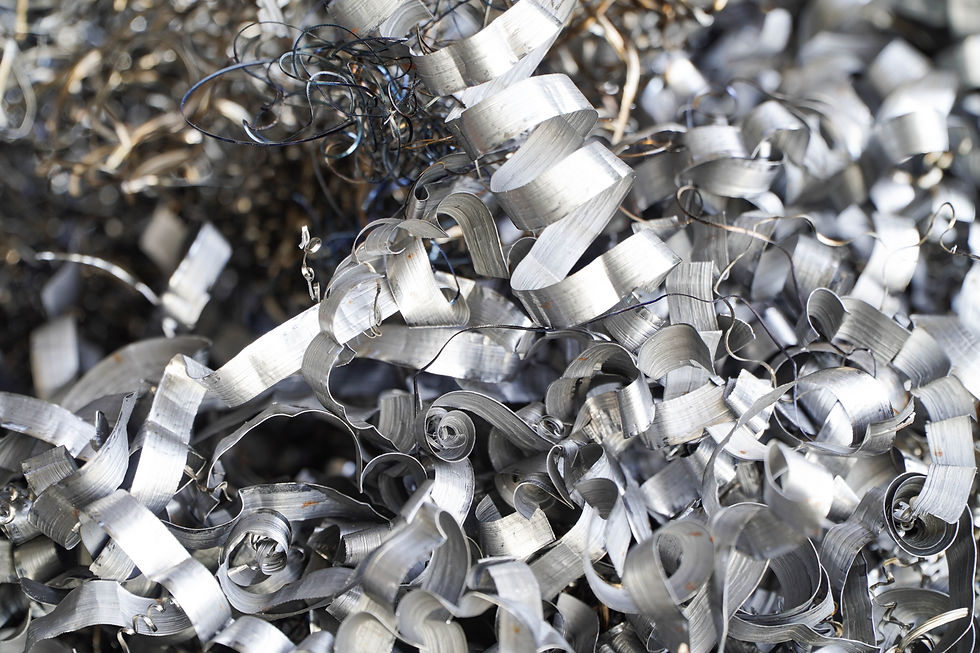
Here are real-world examples of companies implementing sustainable practices similar to those described:
Fastener Manufacturer Reducing Scope 3 Emissions with Recycled Steel: Böllhoff Group, a global fastening technology company, has committed to using 100% recycled steel in its manufacturing processes at its La Ravoire site in France by 2025. This initiative is expected to significantly reduce CO₂ emissions in their value chain (Scope 3 emissions) by reducing reliance on virgin steel production, a major contributor to industrial carbon footprints. This demonstrates the feasibility and impact of incorporating recycled materials into C-part manufacturing. (boellhoff.com)
Manufacturers Streamlining Procurement with AI-Driven Platforms: While specific company names are not disclosed, a 2023 study by McKinsey found that companies prioritizing emissions-conscious sourcing reduced supply chain emissions by 20% on average, saving businesses an estimated $15 million annually in logistics costs. This was achieved through strategies such as consolidating suppliers and integrating AI-driven procurement platforms to streamline logistics, reduce administrative overhead, minimize waste from overordering, and optimize transportation routes – all of which are directly applicable to C-part procurement. This illustrates the potential for significant cost and emissions reductions through smarter procurement strategies.
Biotech Company Adopting Bio-Based Plastic Components: Green Elephant Biotech GmbH, a sustainable bioprocessing and labware solutions company, has introduced a range of eco-friendly products, notably their CellScrew system, which offers a sustainable alternative to traditional plastic-based cultivation equipment. They have embraced a plant-based alternative called polylactic acid (PLA), a biopolymer derived from plant starch, which meets regulatory requirements and is biocompatible. Choosing PLA reduces reliance on crude oil and significantly lowers carbon emissions, even in end-of-life scenarios that require incineration. This demonstrates the viability and benefits of using bio-based plastics in various applications, including potentially for certain C-parts. (techtarget.com)
These examples illustrate how companies across various industries are implementing sustainable practices to reduce environmental impact and enhance operational efficiency. They offer concrete evidence of the benefits achievable through strategies like recycled materials adoption, AI-driven procurement, and the use of bio-based plastics – all relevant to the world of C-part sustainability.
Conclusion: C-Part Sustainability as a Competitive Advantage
The transition to a circular economy depends on embracing sustainable practices at every level of the supply chain. C-parts, though often overlooked, represent a significant opportunity for businesses to contribute to a more sustainable future. By prioritizing sustainable materials, leveraging technology, and collaborating with responsible suppliers, businesses can not only reduce their environmental impact but also drive innovation, enhance brand value, and secure a competitive advantage in the evolving landscape of sustainable manufacturing. The choices we make about even the smallest components will define the legacy we leave behind.