Welding Processes – Understanding the Difference: TIG, MIG & More
- Cori Brazie
- Nov 9, 2020
- 3 min read
Welding is an essential tool for a wide variety of fabricators as it facilitates the joining of two or more pieces of metal together. Through the extreme heat that is produced during welding, the metallic structures of the metals fuse together, making an incredibly strong seam. There are a variety of different welding types, each suitable for different situations.
Read on to learn about the most common welding methods. It’s important to know which welding application will be best for your specific application.
Understanding Welding
The term welding is actually a very general one, only referring to the result rather than the process, which is fusing two metals together. When many people think of welding, they are probably imagining the classic image of a man in a mask, holding a welding torch to join metal. That specific welding process is called fusion welding.
During fusion welding, the edges of the two metals to be joined are heated above their melting point in a very small area. This classic welding method provides a good example of the general idea behind welding.
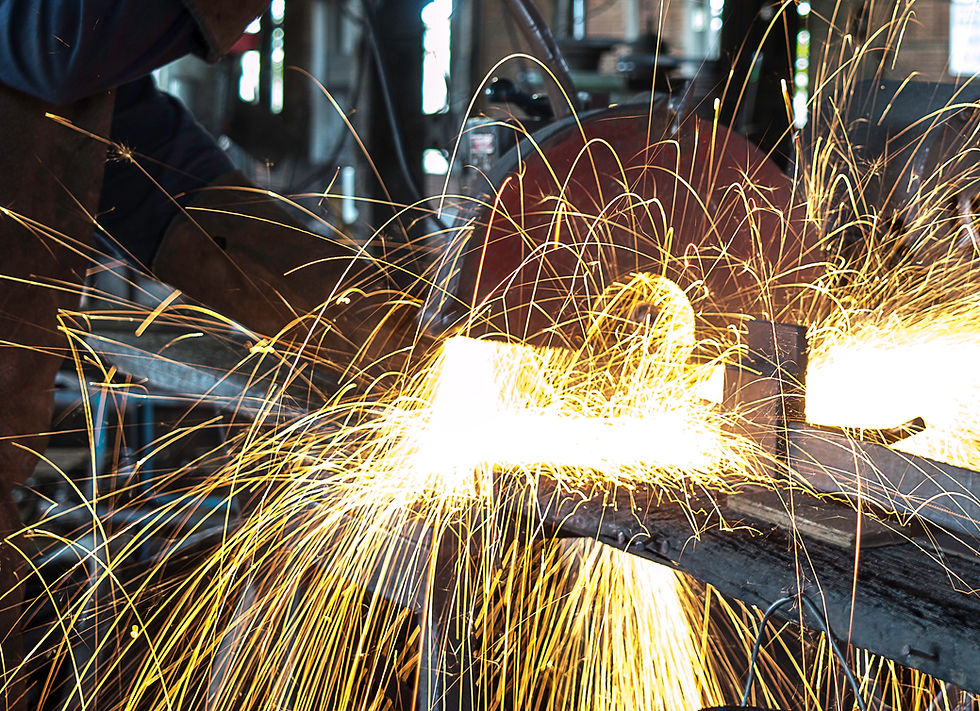
By melting the two metals, it forms what is called a weld bead or weld pool—a small spot of liquid metal.
The welder pushes this weld bead all along the seam of the metal.
As it cools, metal pieces are joined.
The metals being joined can be different material types, but they must be chemically compatible enough for them to mix when melted or the weld will eventually fail.
The Different Types of Welding Processes
While that explanation of welding may sound simple enough, there is a world of complexity in how welds get created. There are several different welding processes that are typically used, including MIG, TIG, Stick, and Resistance Spot Welding.
MIG Welding
Metal Inert Gas (MIG) welding creates an electrical circuit through the two objects that are being welded and a welding wire. An electric arc is created by placing the wire a short distance away from the surface of the metals. This electric arc has a temperature of thousands of degrees, and it melts both the wire and the two metals together. A shielding gas protects the weld from the air until the operation is completed.
MIG welding is very commonly used in industry and manufacturing, especially in the automotive sector. It can provide a strong weld for very thin materials, making it useful in many situations. MIG welding also works well on steel, so it is also very commonly found in construction applications for structural steel.
TIG Welding
Tungsten Inert Gas (TIG) welding is a more complex process than MIG welding, but can also be much more precise. In TIG welding, instead of using a consumable wire, the welding gun uses a tungsten metal rod to create the electrical arc. The filler rod is held in the other hand to melt the metals together.
TIG welding is typically used to weld aluminum and alloys, and often results in a higher quality weld than MIG welding. As with MIG welds, a shielding gas protects the weld from the air.
Stick Welding
In stick welding – also known as Shielded Metal Arc welding – the rod being used as the electrode is coated in a protective material. As the protective material is heated, it evaporates and forms a shielding gas to protect the weld. This welding process is the simplest, and thus used extensively to weld iron and steels during industrial fabrication.
Spot Welding
During spot welding, two pieces of metal are held together under pressure and electric current is concentrated in a small spot, creating a tiny weld bead. This type of welding is especially good for welding sheet metal and wire mesh, and it is very common in assembly line applications.
Materials Used for Welding
At Blue Grass, we weld steel, stainless steel, aluminum, brass, and copper. There isn’t an easy answer for which type of welding is always best suited for each metal, but our experienced staff can help you weigh the advantages and disadvantages of each type and choose the best method for your application.
MIG welding is best suited for:
Carbon steel
Stainless steel
Aluminum
Stick welding can be used on:
Steel
Iron
Aluminum
TIG welding can weld the wildest variety of materials, including:
Steel
Stainless steel
Aluminum
Magnesium alloys
Copper and copper alloys
Titanium
By understanding the different types of welding processes, you can make an informed decision on which will best suit your application. Please contact us or request a quote to learn more about how Blue Grass can help you with your welding needs.